How PC cases are made: inside NZXT's factory
We travel to China to visit NZXT's case factory to see the people (and giant machines) that build our PC cases.
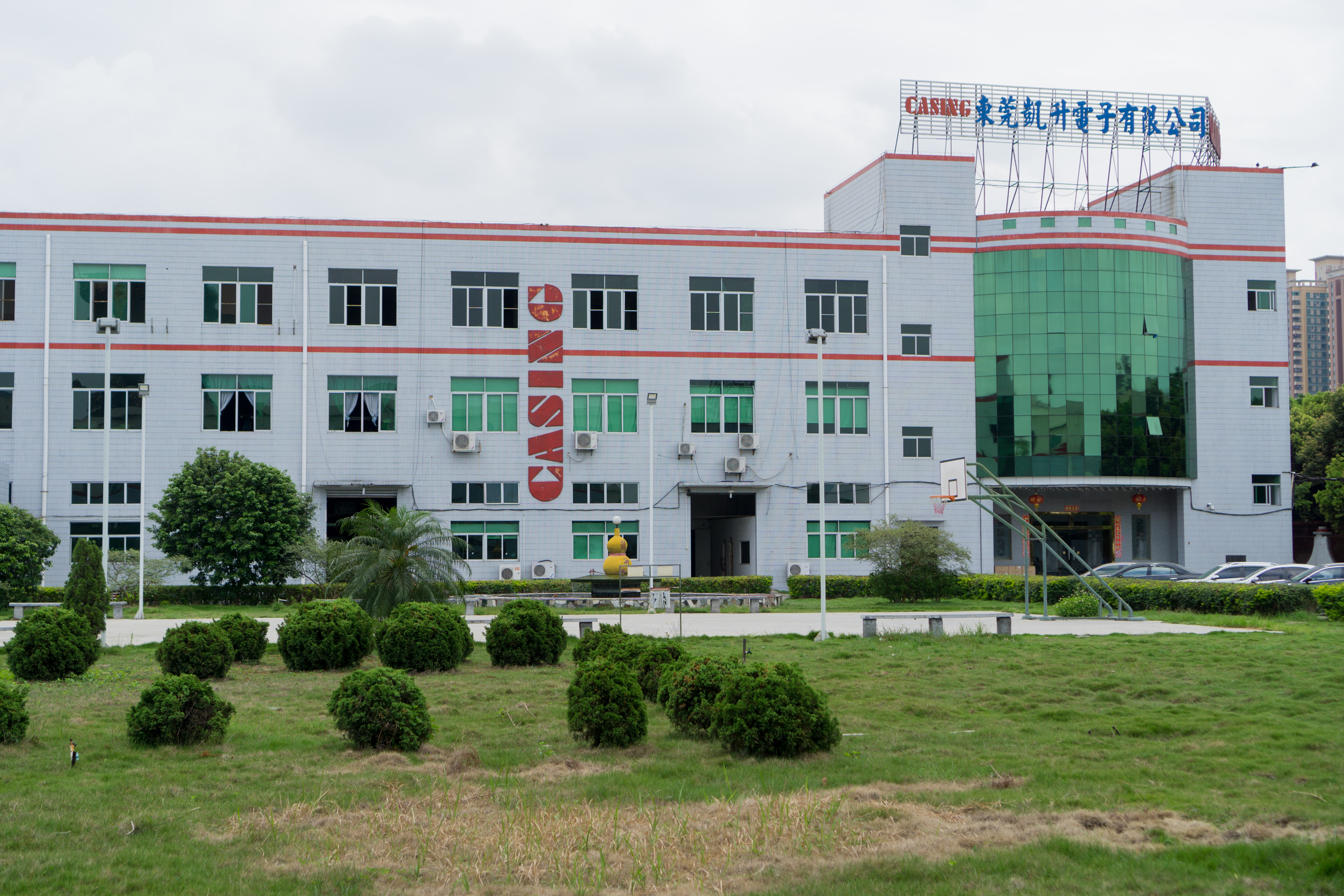
Chances are good that most of your PC was built in or around Shenzen, China, a mecca of electronics manufacturing. I took a trip to nearby Dongguan, a short drive outside of Shenzen, to visit a factory your PC definitely came from if it's housed in an NZXT case. This factory, built in 2000, devotes most of its manufacturing energy to NZXT's PC cases, and I got to tour the facility and check out every step of the process.
In the following gallery, I'll dive into how cases are built, how surprisingly manual the assembly line process still is, painting, quality control, assembly, and more.
Want to see the factory in action? Check out our video tour right here.
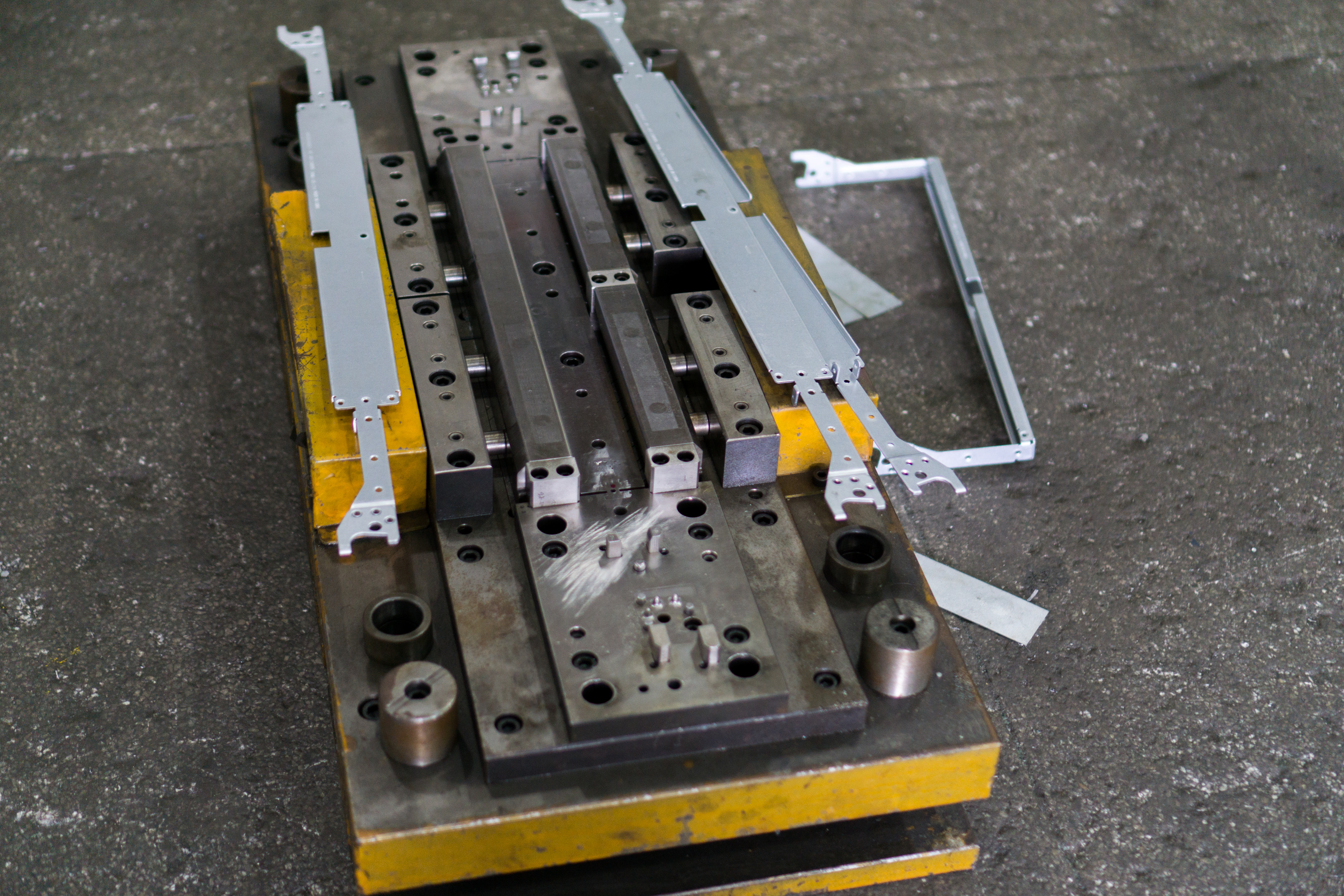
Pictured above is a 'tooling' used in manufacturing. A tooling is, essentially, a mold used to give form to metal or plastic parts, like a PC case. Think of it like a really precise, really heavy steel cake pan.
Toolings are placed on large metal presses in the factory (you'll see those in a few slides), and then the raw metal is placed within and pressed into shape. Unlike a cake mold, though, you can't make a whole PC case with a single tooling. It takes dozens of them to shape each small bend, indentation, drill hole, and cut in the metal that makes up each side panel and frame and interior geometry.
The average NZXT case can take between 60 and 70 toolings to put together, but more complex cases require even more. The Manta, for example, requires over 100. And that's just for final production, not counting the multiple prototyping phases a case goes through in the design phase. All told, designing the toolings for a case can cost in the range of $150,000.
Typical lifespan of a tooling? That depends on what it's stamping out. Plastic parts, an average of 250,000 units. Metal stamp toolings have slightly shorter lives of 150,000 units. After that, they'll need to either be fixed or replaced entirely. Tooling can also be made to last longer—it all depends on how many units a manufacturer wants to produce. A high-yield tooling typically lasts, at most, up to 500,000 units.

A worker refines the surface of a metal tooling. The measurements need to be extremely precise for mass production to ensure components fit together properly. This could be the tooling for a brand new case, or a new tooling to replace one before its lifespan runs out.
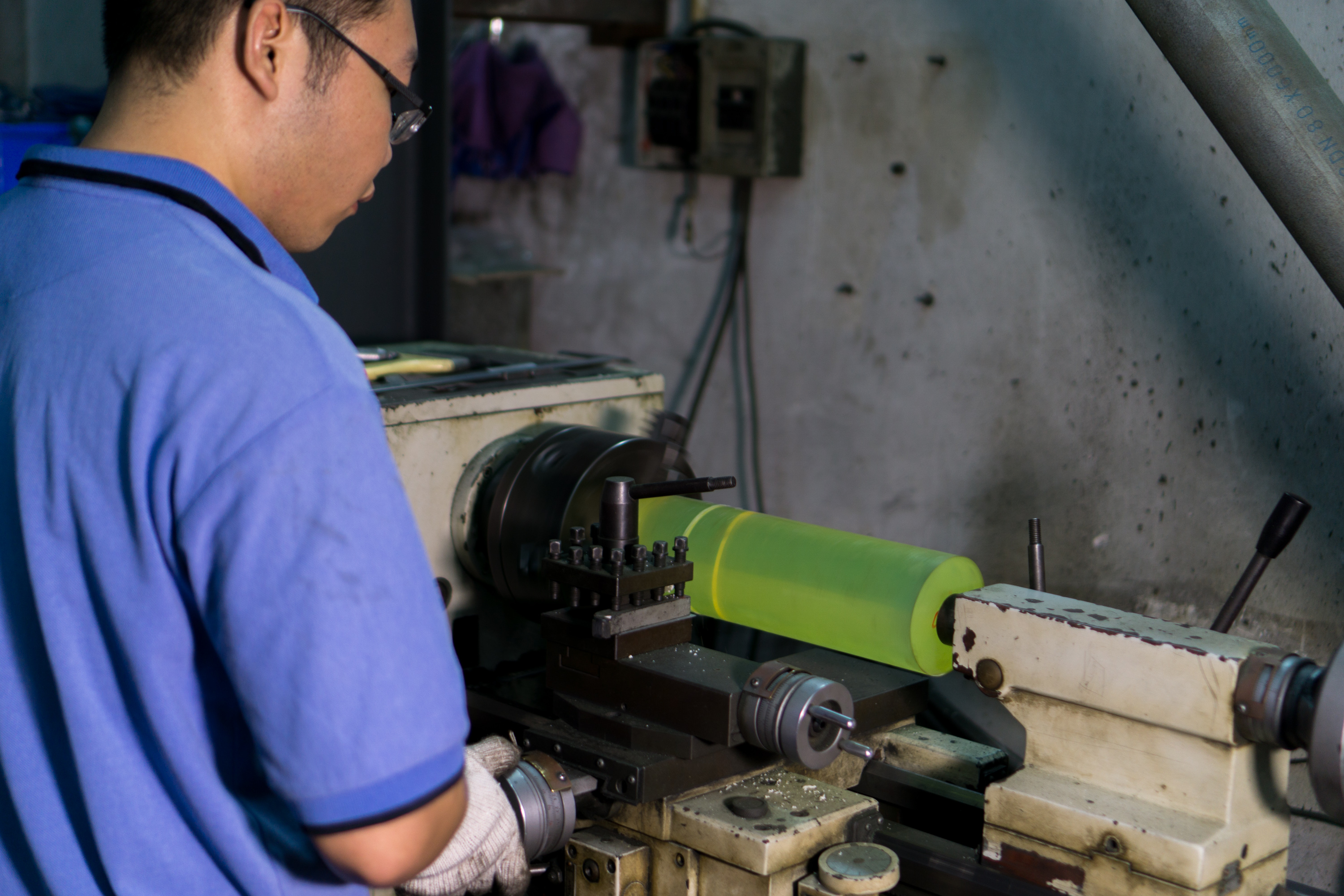
This green polyurethane plastic cylinder is being cut to aid into the manufacturing process. When pressing large metal parts, it's important that weight is evenly distributed so the metal never dents or sags. The plastic spools help ensure even pressure distribution without damaging the metal.
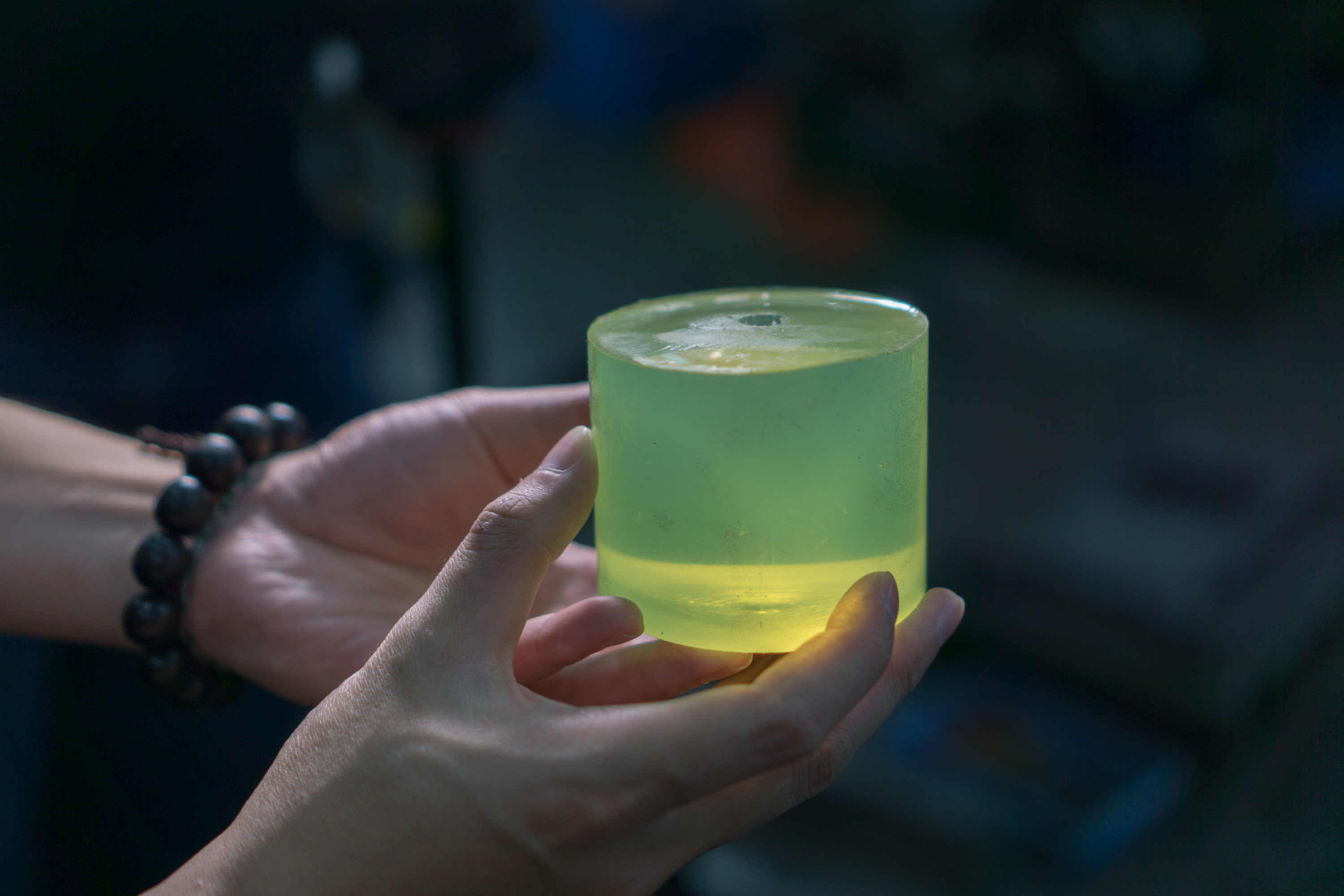
A close-up of a cut piece of polyurethane. As you'll be able to see in the next image, they're also used when storing toolings.
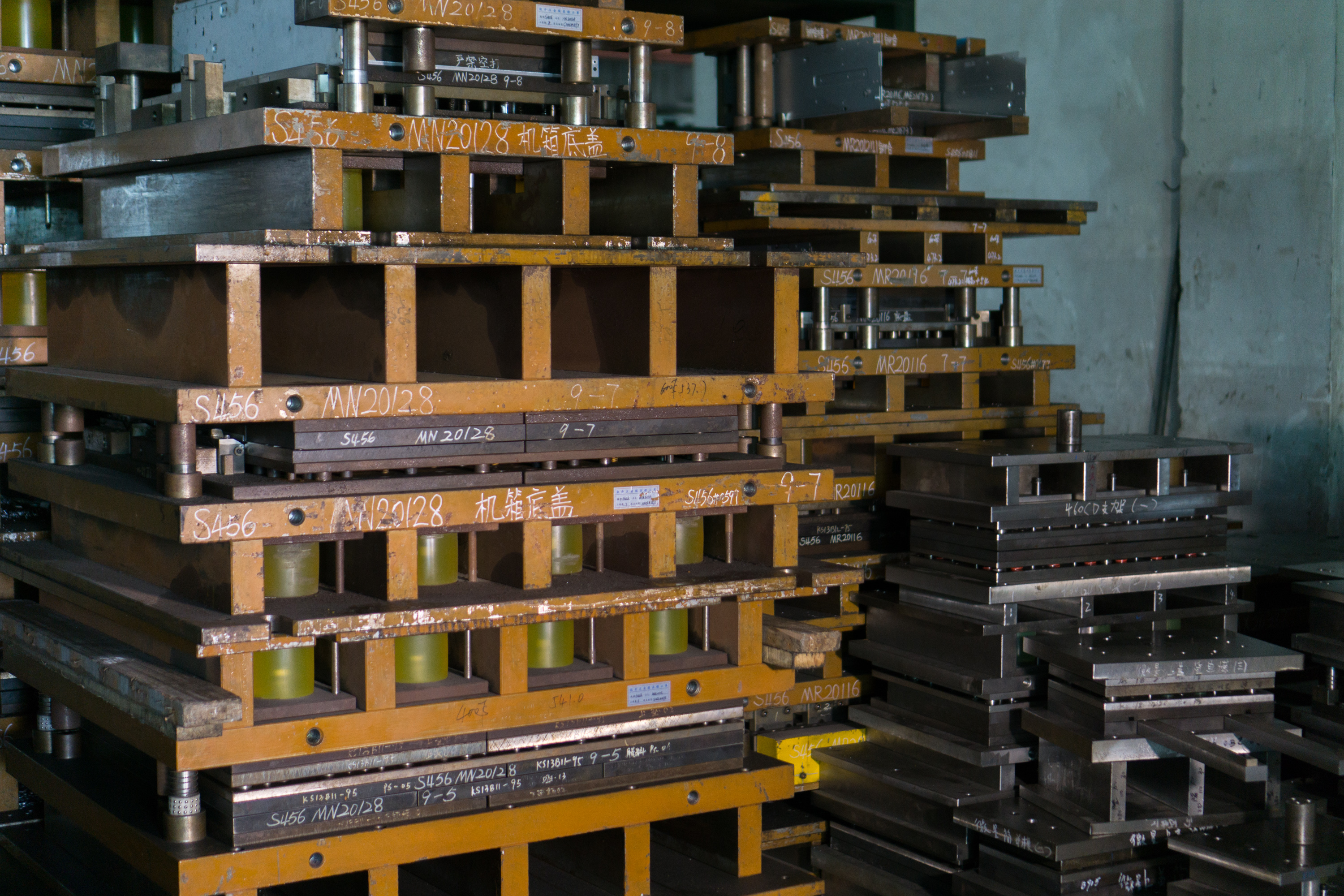
A small selection of the case toolings being stored at NZXT's factory. You can spot the poly suspension bushes stored with them. NZXT's product catalog is too big for all of its cases to be in production simultaneously, so the toolings must be safely stored between manufacturing runs.
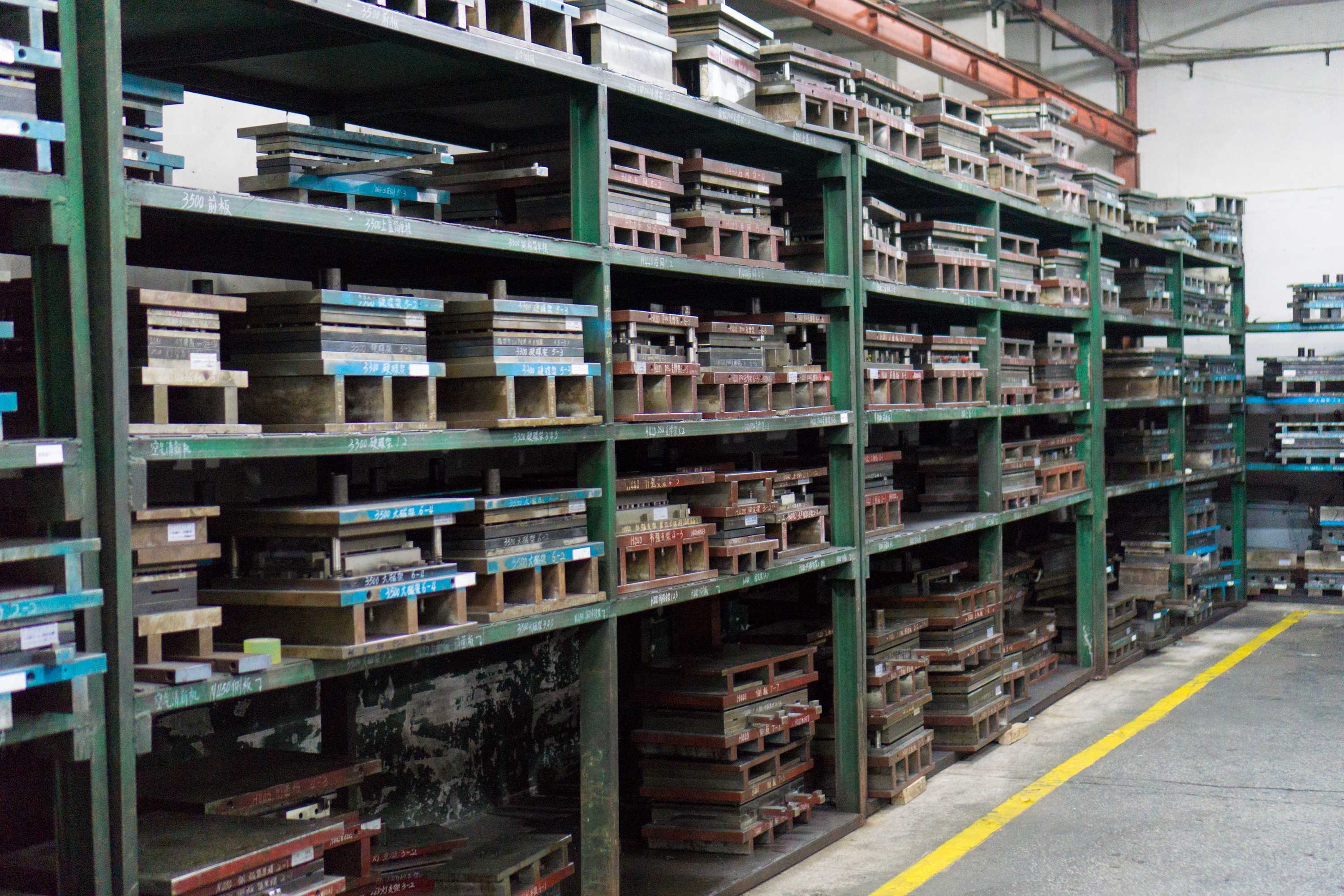
Toolings, toolings, and more toolings. Remember, a single case can take as many as 100 of these, and each one is a big, precision-cut slab of steel. There are well over 1000 toolings stored at NZXT's factory.
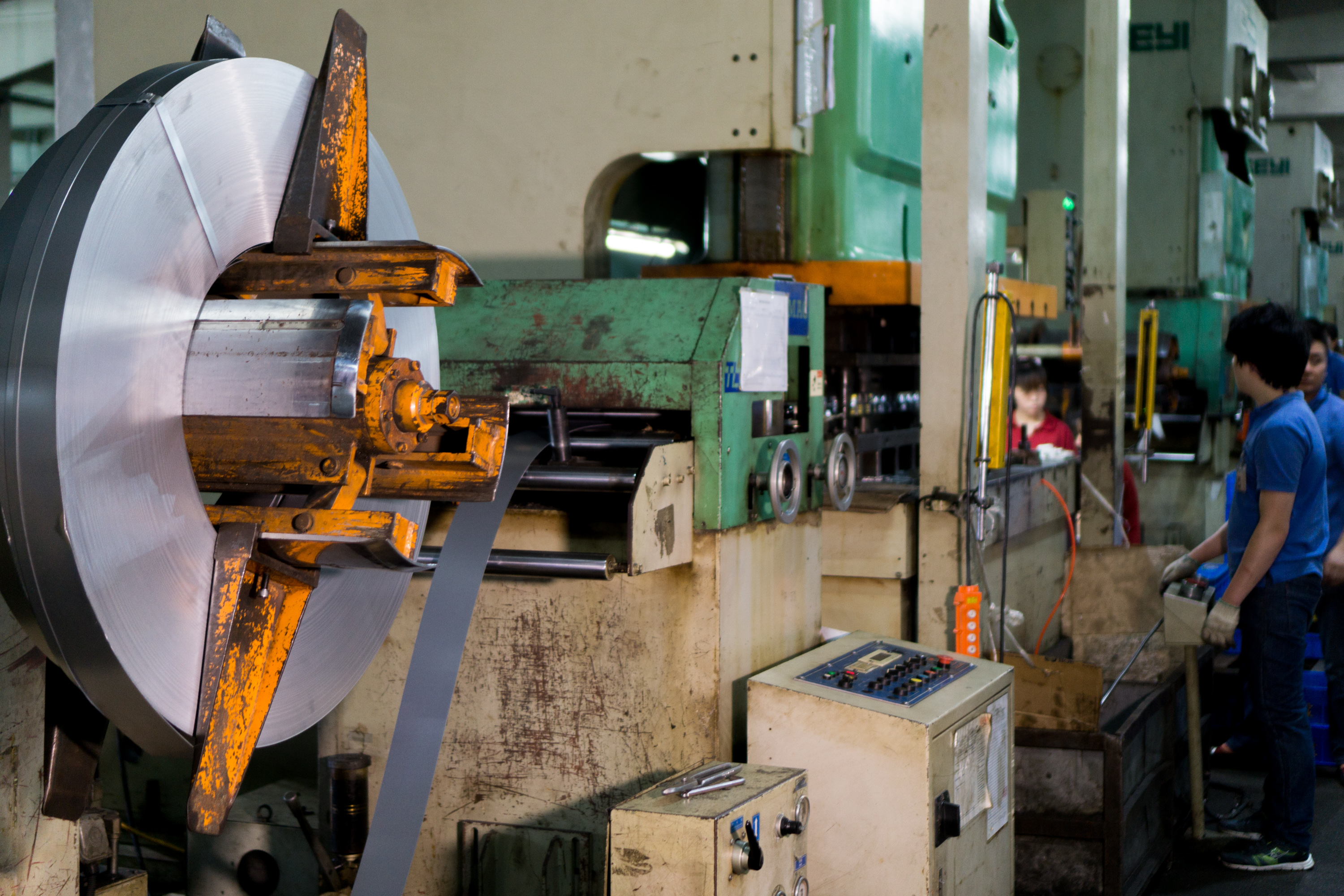
Here a giant spool of steel is fed into a hydraulic press, which will bend the sheet around a case tooling to form the beginnings of a component. It's automated and presses down every three seconds or so.
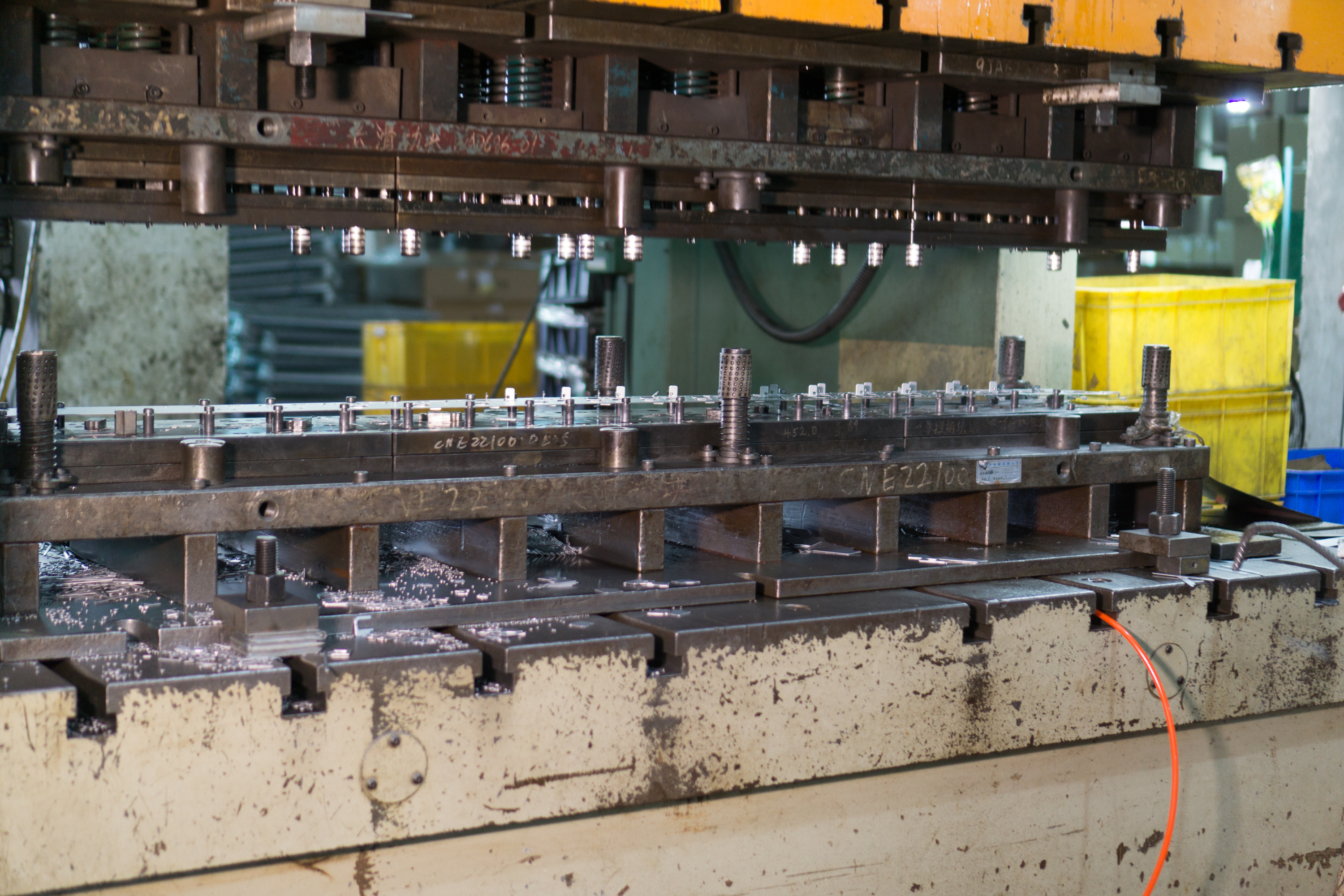
Here's a closer look at the press. Notice all the metal debris being punched out and falling below. The press is outfitted with a tooling, with metal fed through by the machine pictured in the last image. A worker watches over it out of frame.
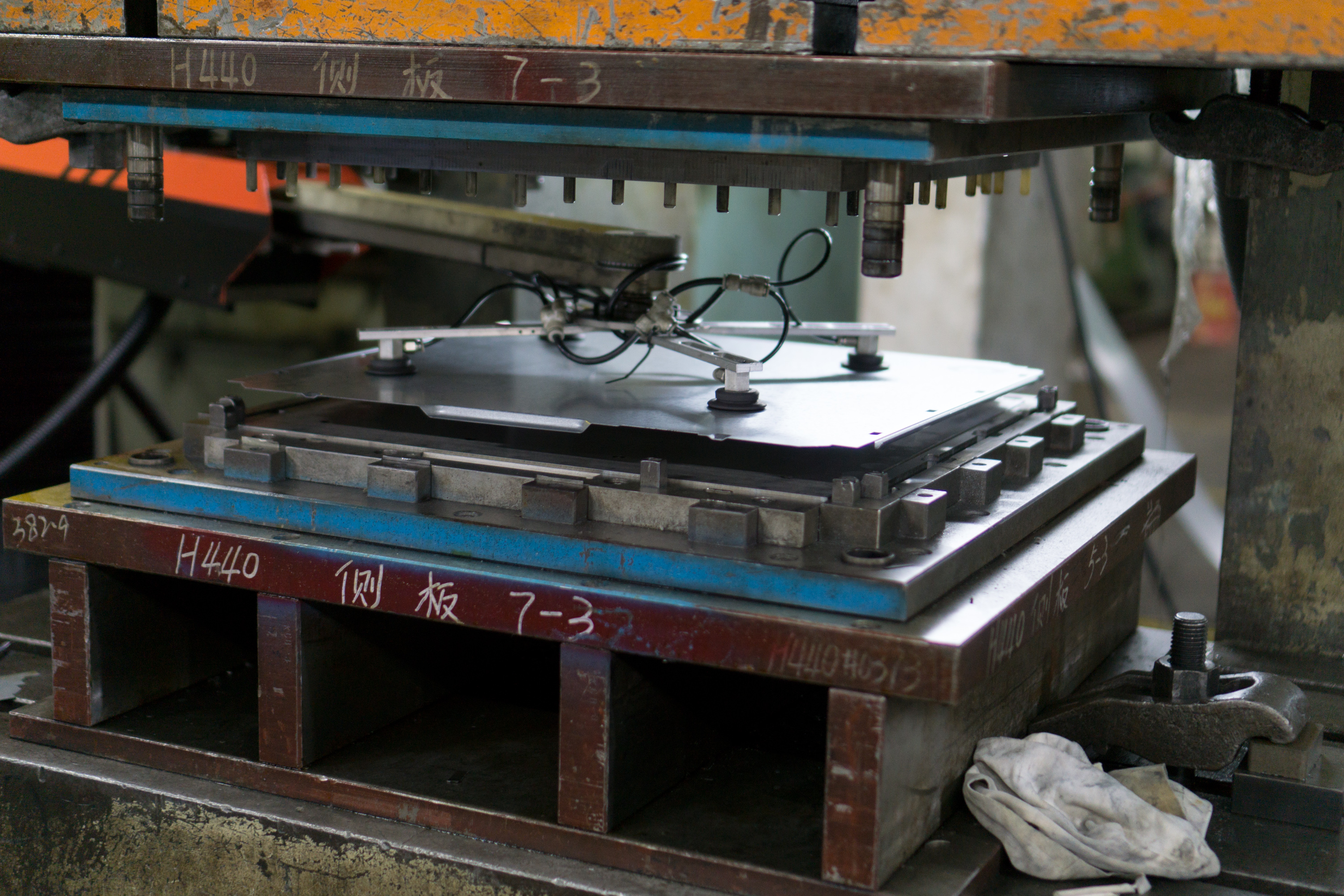
Here a robot arm grabs a PC case panel and moves it from one press to another. Each press has its own tooling set on it to shape a different element of the case. If you look at the writing on the tooling, you'll notice it belongs to the H440.
While part of the assembly line used these robot arms to move components between toolings, much of it was done by hand, as you'll see in the next images.

A worker removes a side panel from a press after it's been punched into shape by its tooling. Unlike the first press we saw, this one is activated manually, so don't worry about his hand.
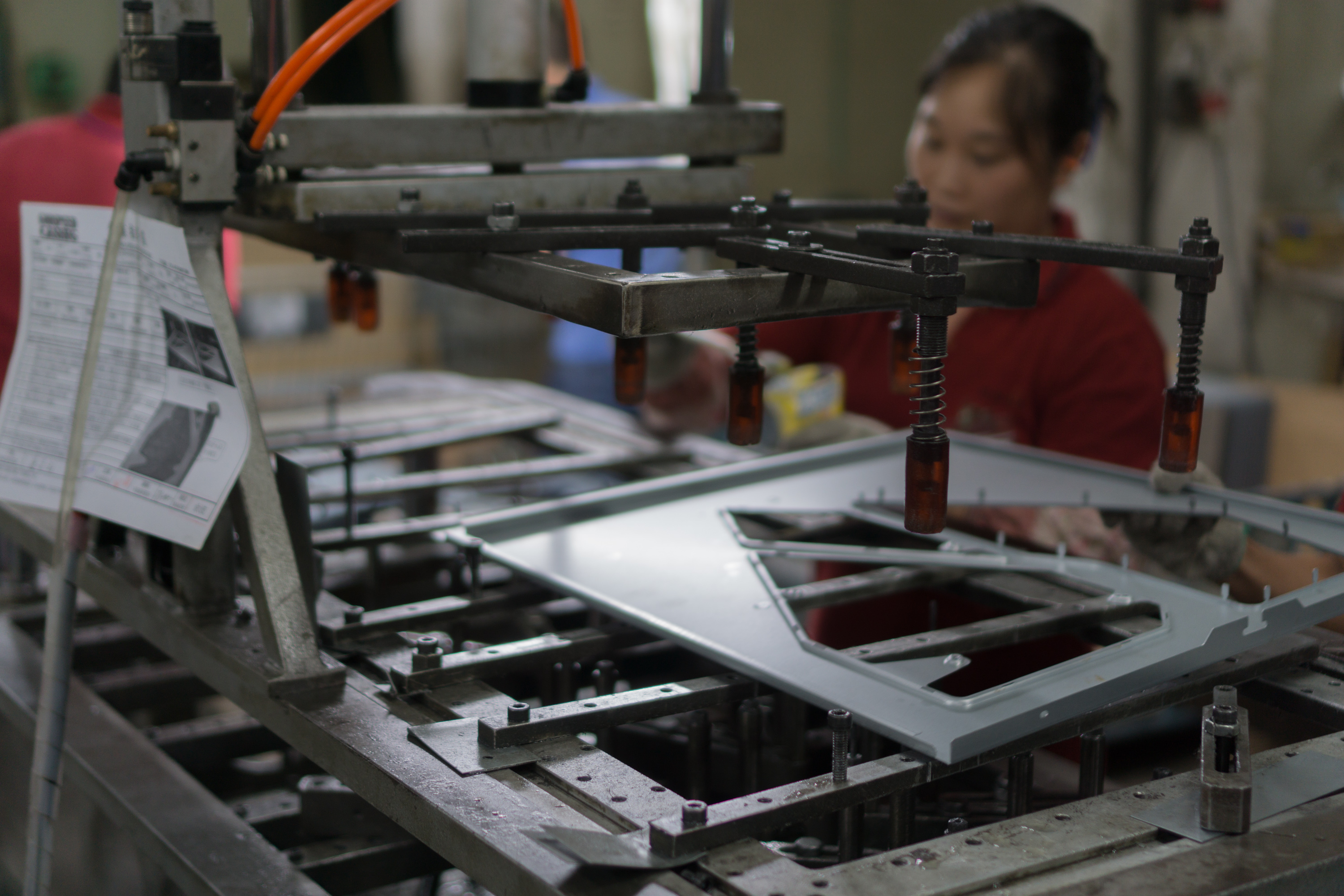
Here you can see the same type of side panel from the last image on another manually operated machine. This one is used to drill pilot holes for later assembly. Look closely and you can see the drillbits coming up from the bottom of the machine.
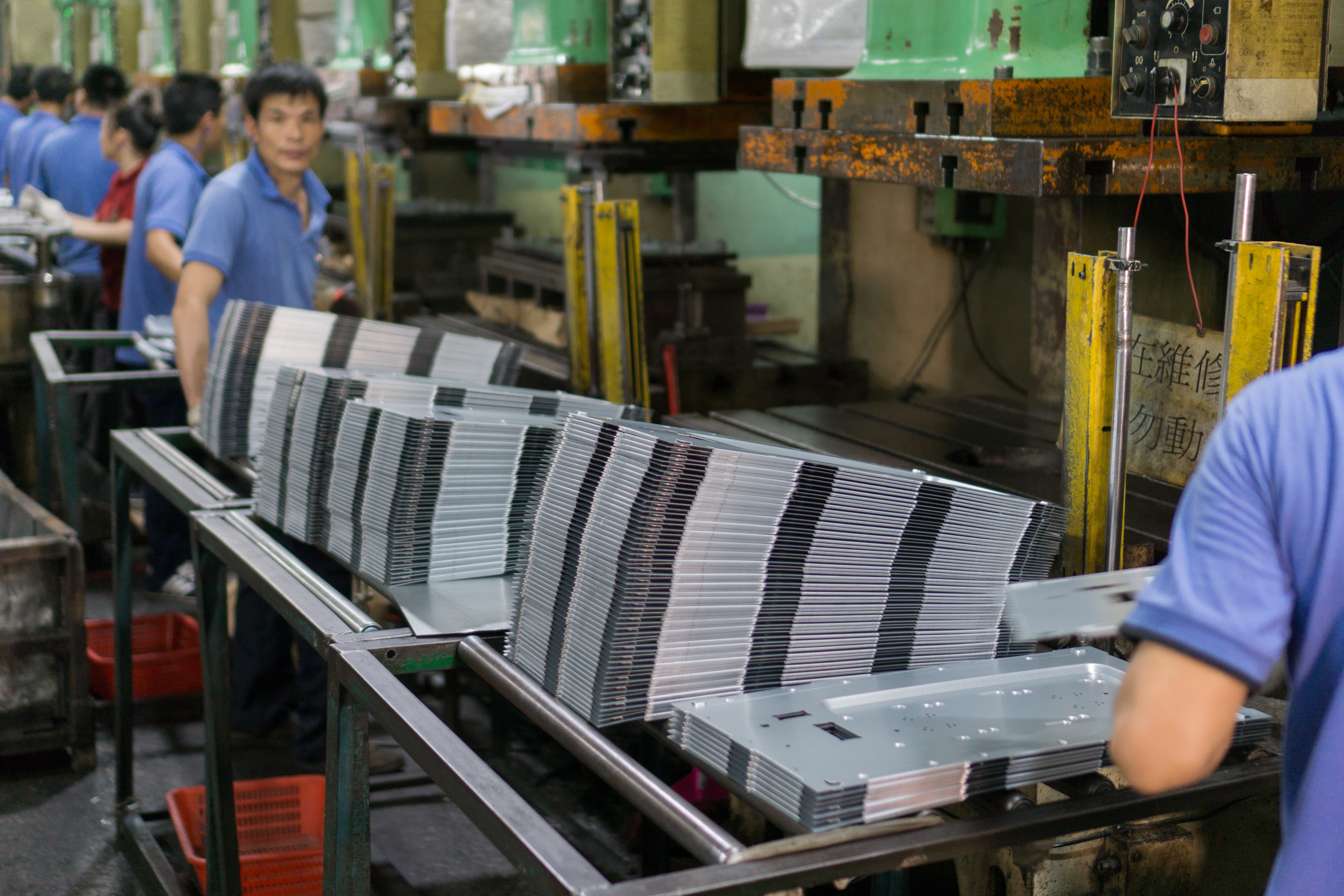
Now there's an assembly line! You can see a row of presses stretching down the line, each with a separate tooling equipped. Stacks of panels come out of the tooling and are then moved down for the next step of the manufacturing process.
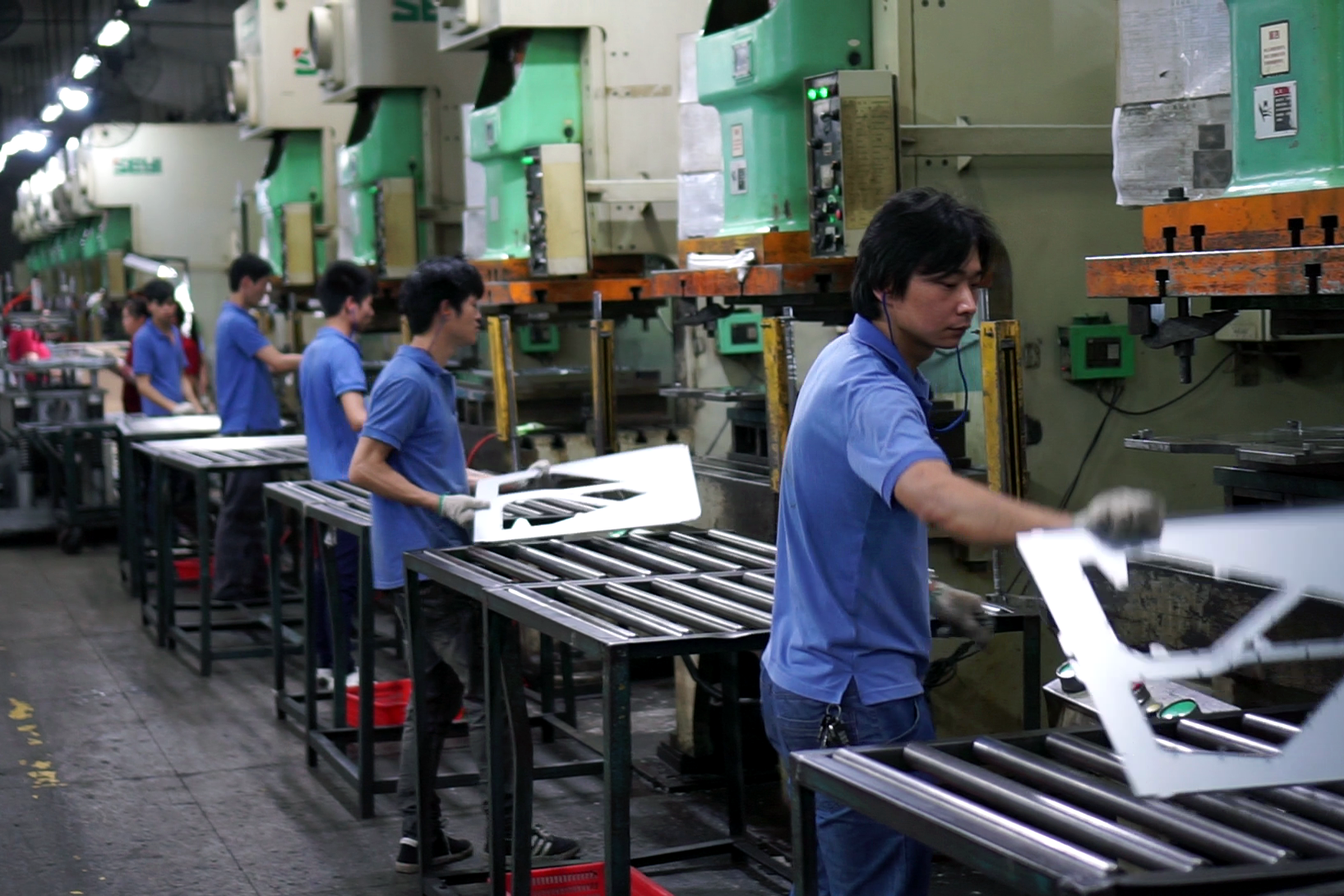
A long shot of one of the manufacturing rows, where workers pass a case side panel down the line to be punched.
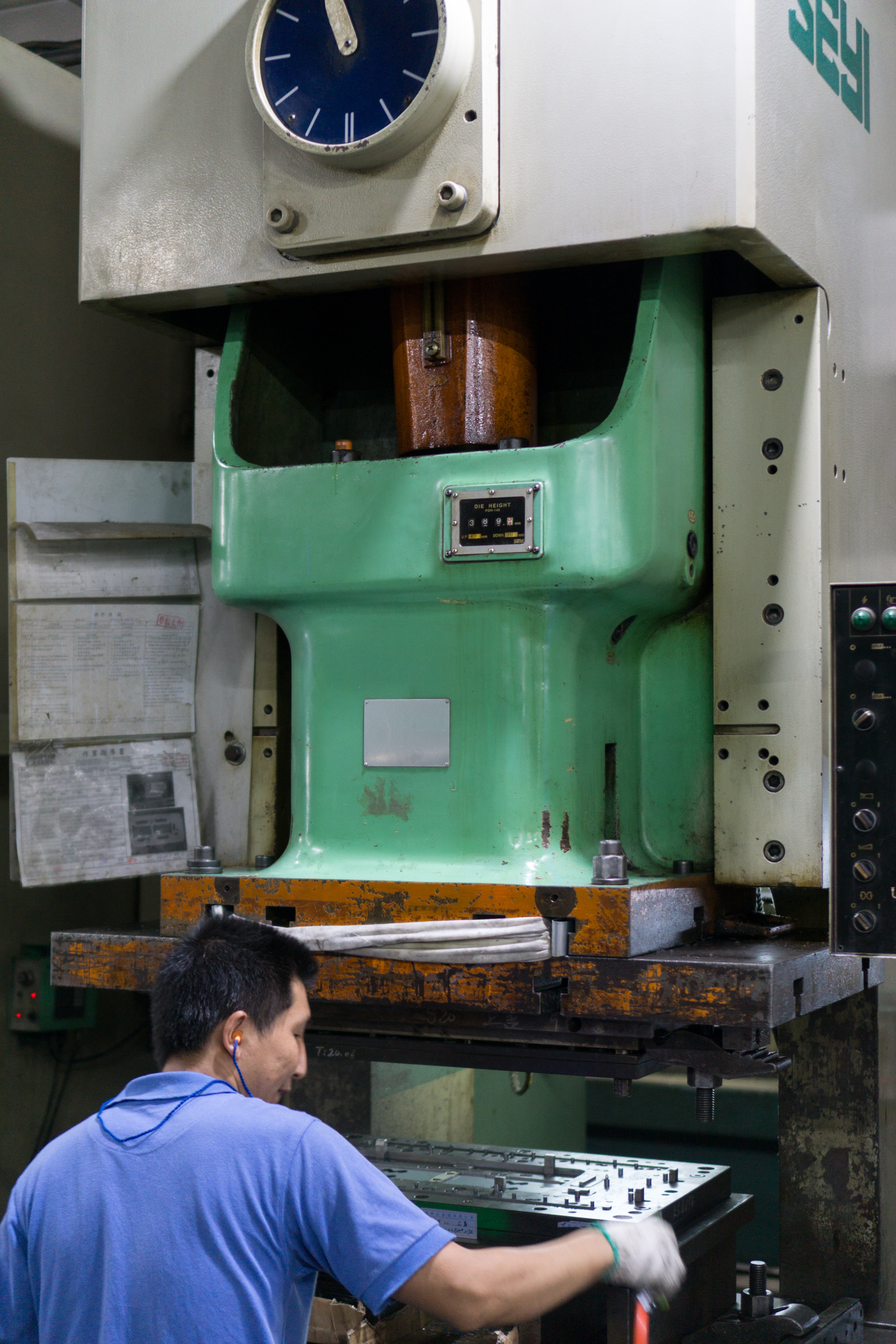
A better perspective on how huge these machines are. You can read more about them, and similar presses, on manufacturing company SEYI's website.
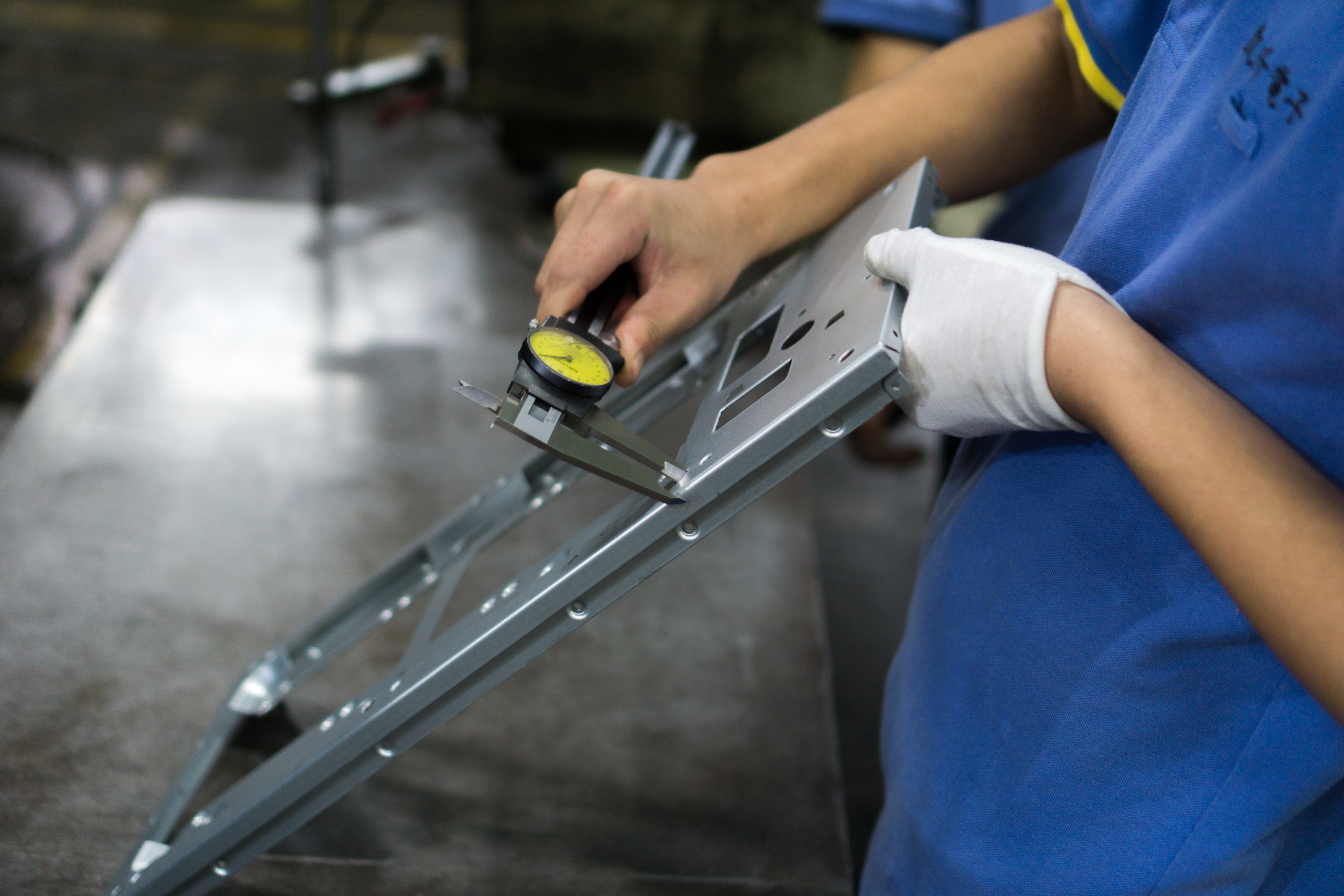
Quality control is performed at multiple points in the manufacturing process. This is a line check—a worker grabs this panel off the stack and measures it to ensure it was formed by the tooling properly. Each measurement needs to be precise, down to the sub-millimeter.
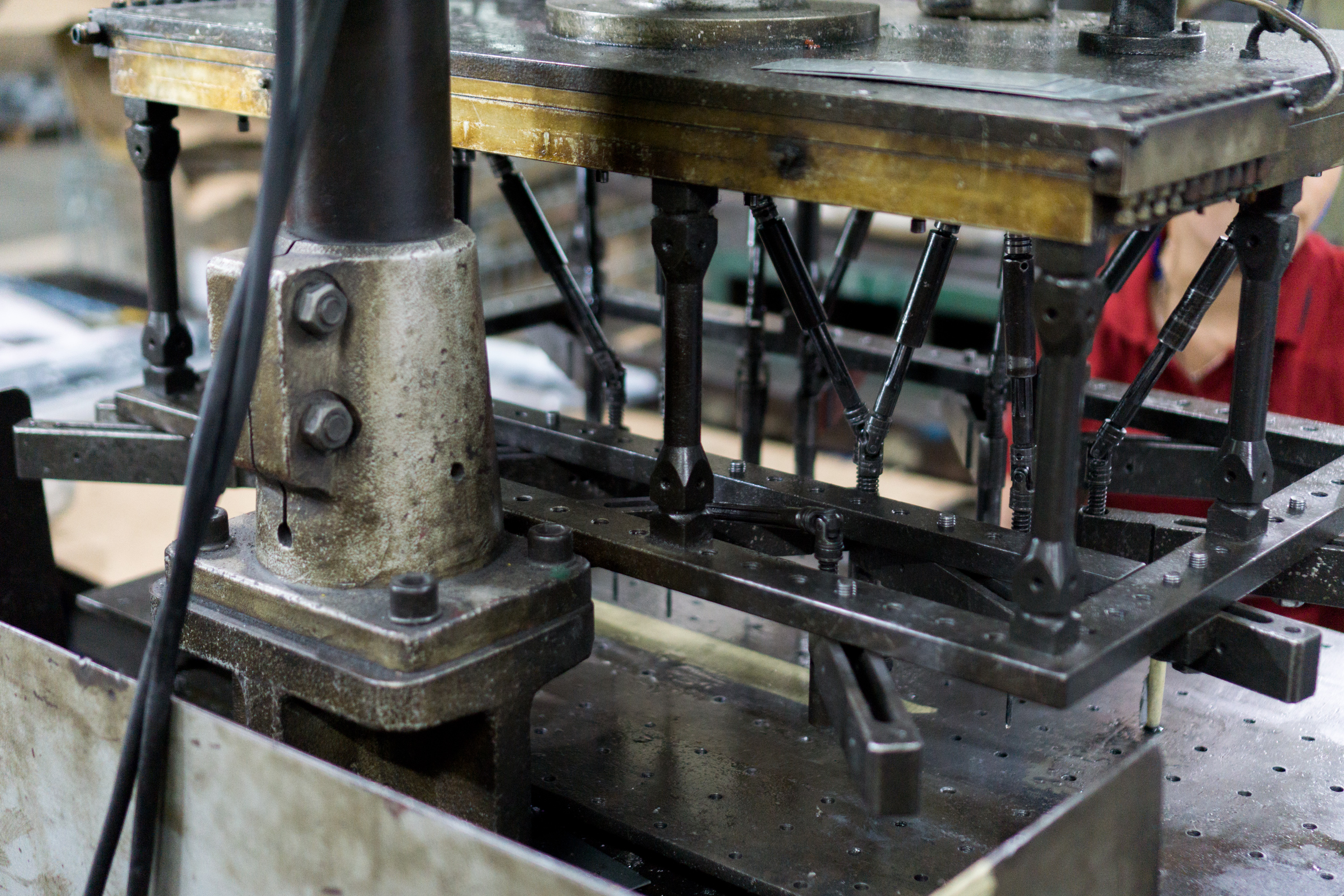
Another machine used to pre-drill holes in a case prior to assembly. In this instance, the case in production was the Phantom 820, which we'll see more of later.
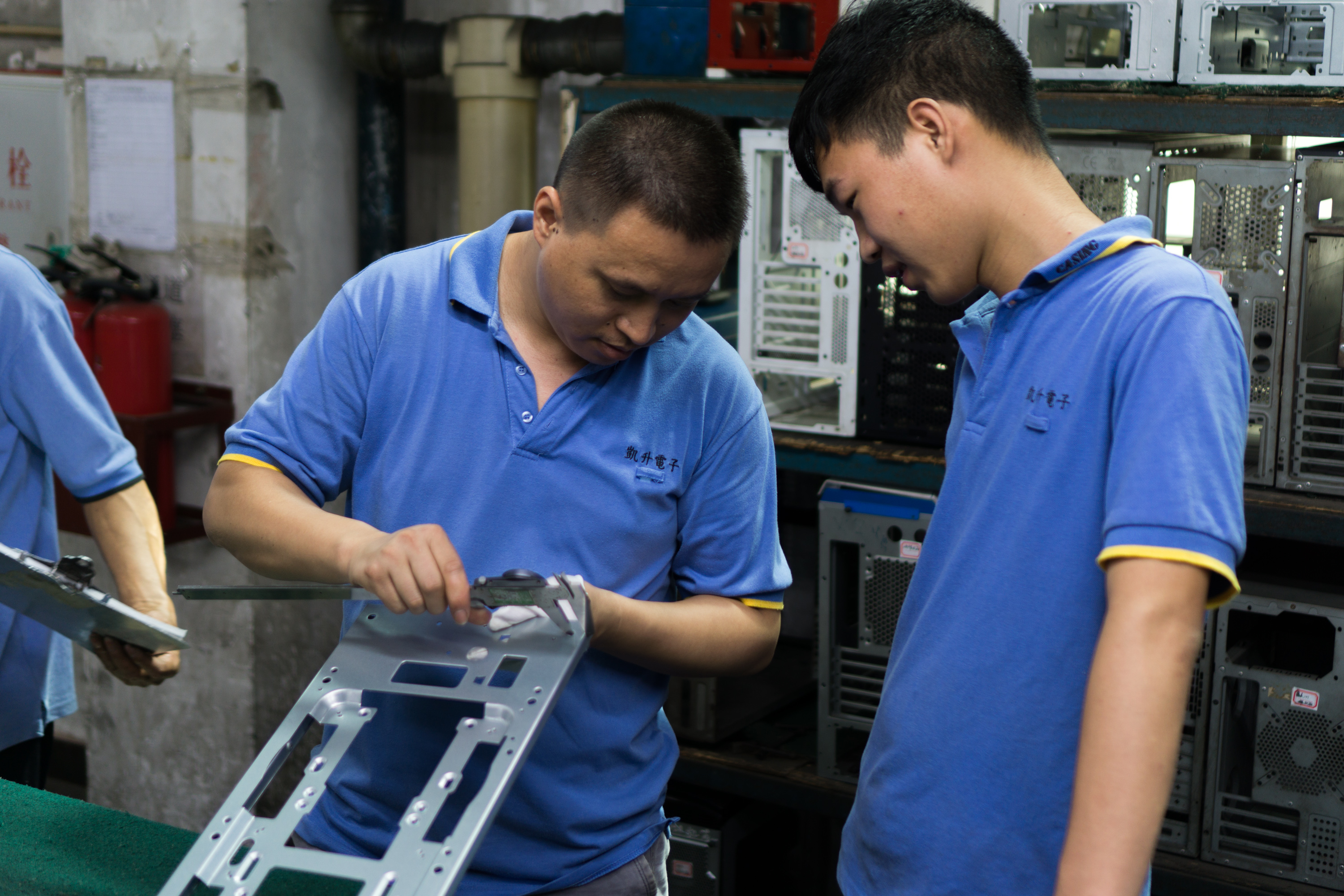
The main quality control station following the production line. Here several workers vet a selection of components before they head off to the next stage: painting!
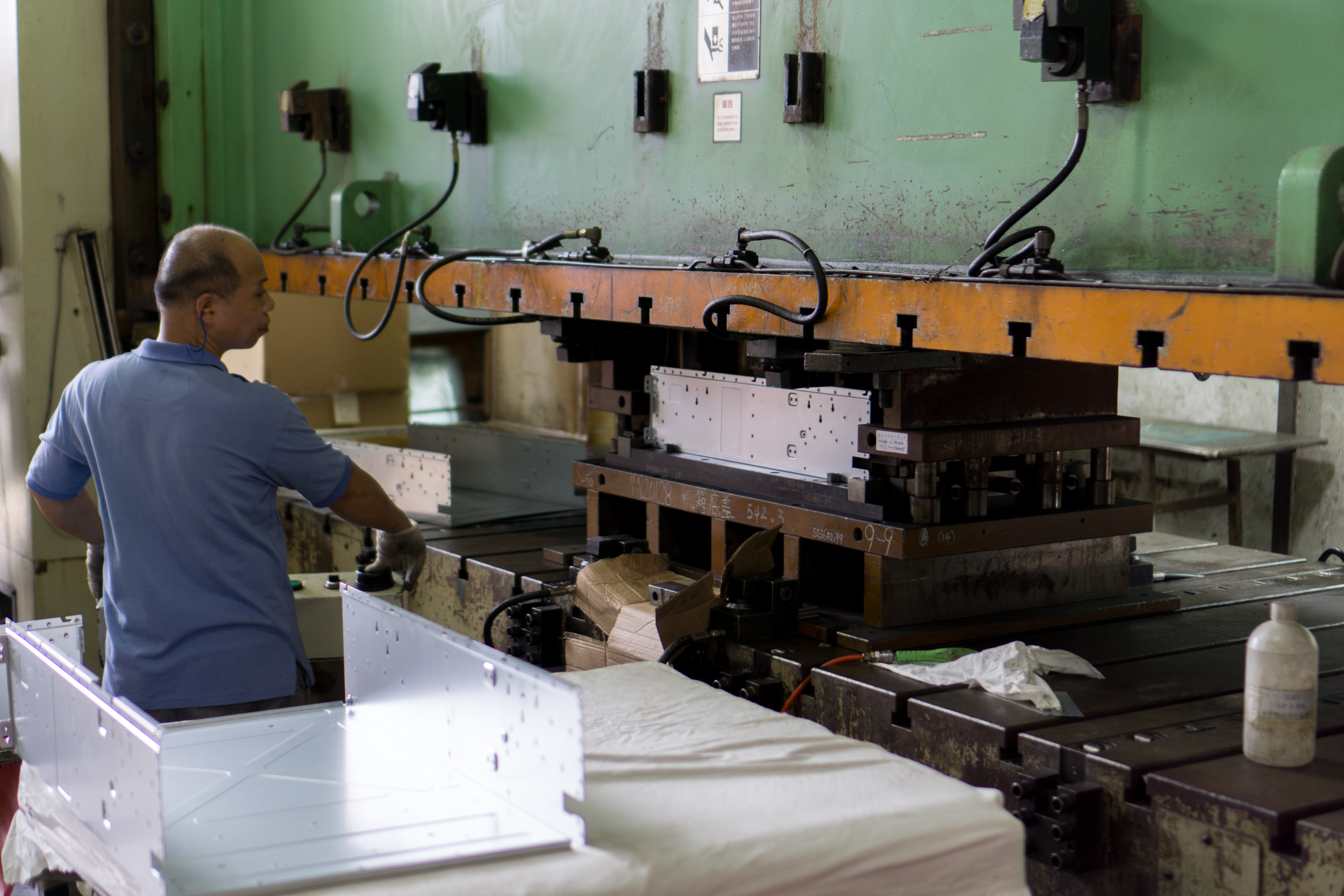
Away from the longer assembly line were two larger presses used for bigger components. How much larger?
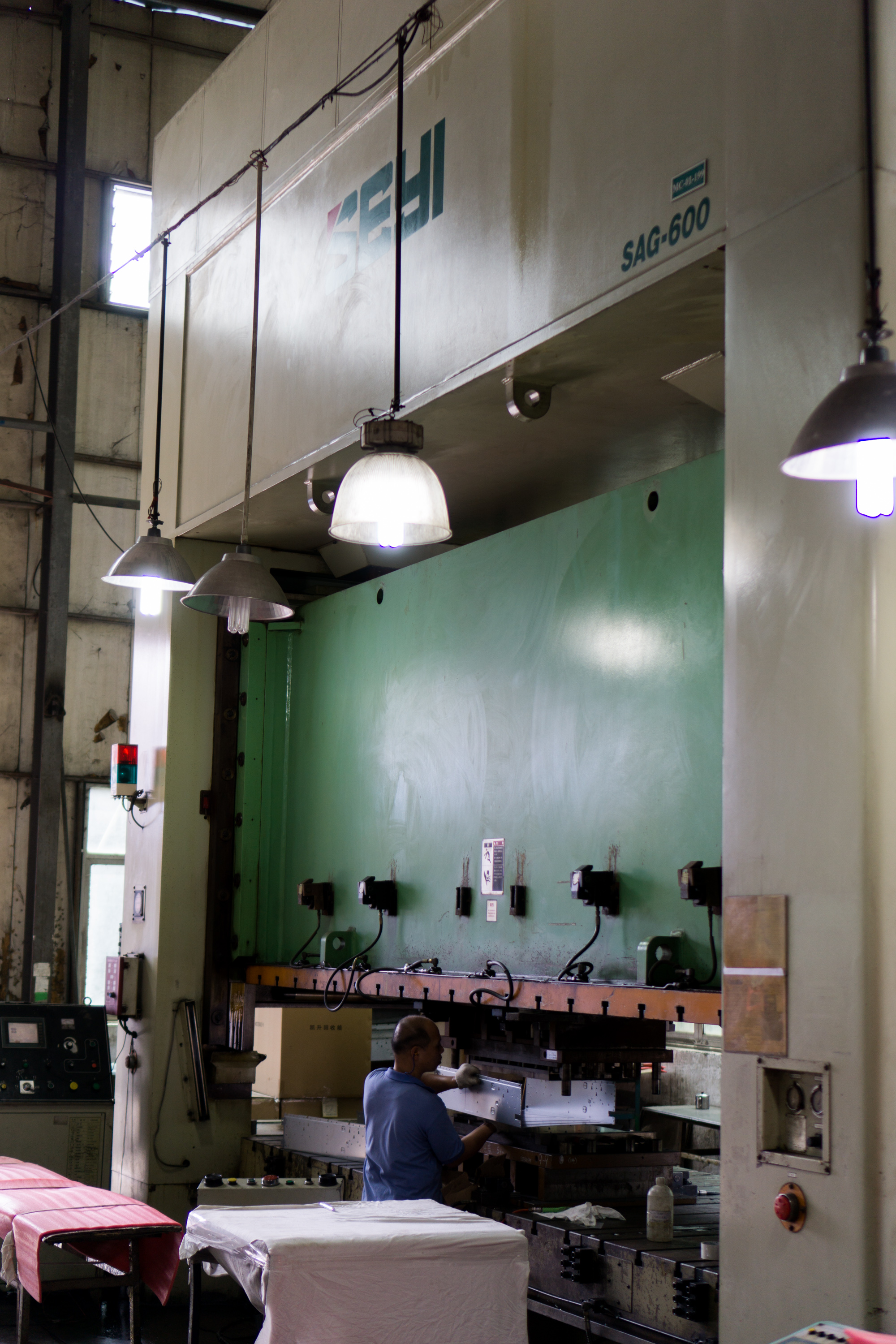
Yeah, that's a pretty big press. 600 tons of pure mechanical muscle. Don't stick your head in there.
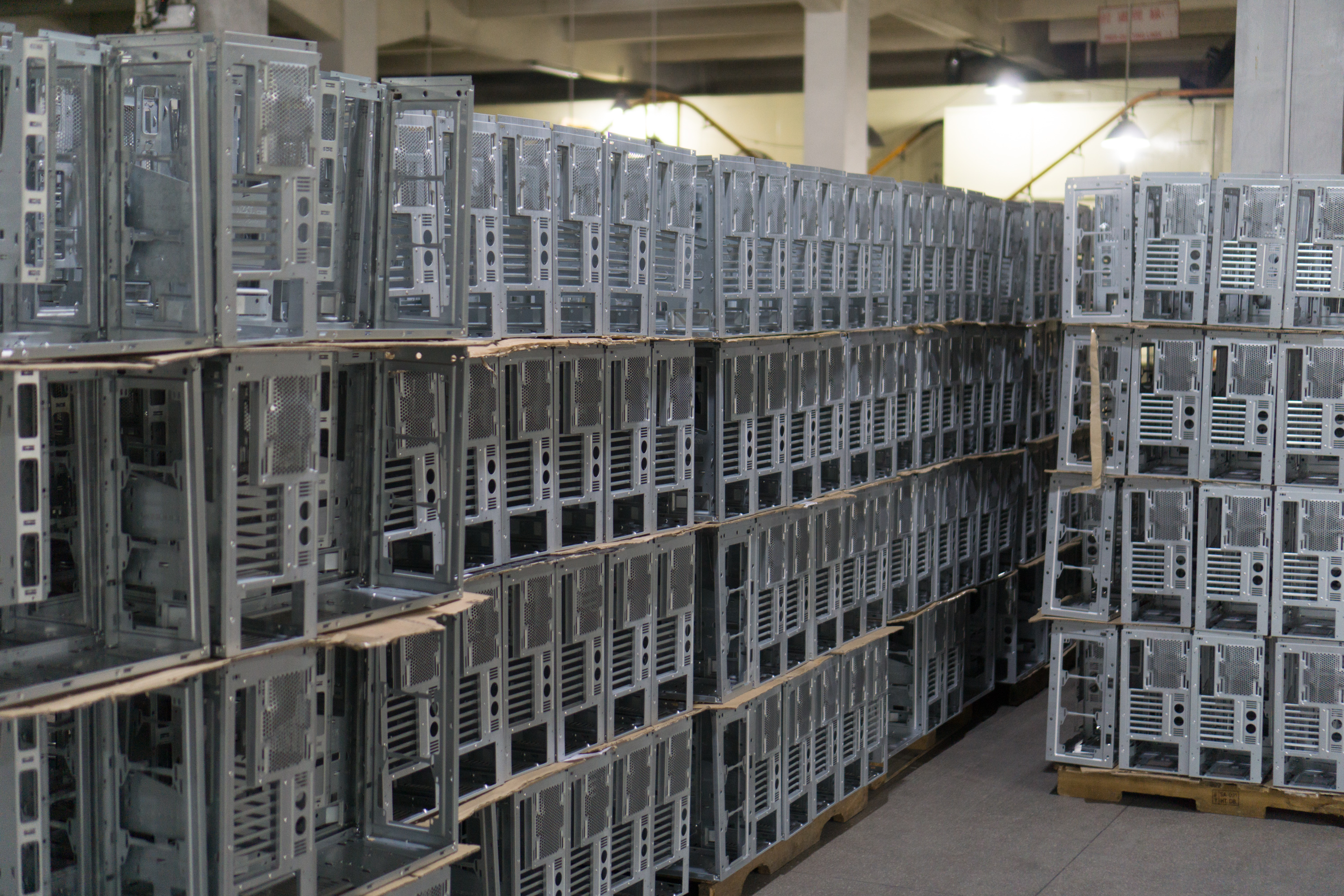
This row of case parts has made it through multiple (probably dozens) of toolings—remember, each separate cut and bend was likely done by a unique tooling along the way. They're stacked up next to the painting area, where they'll soon be given a splash of color to bring them to life.
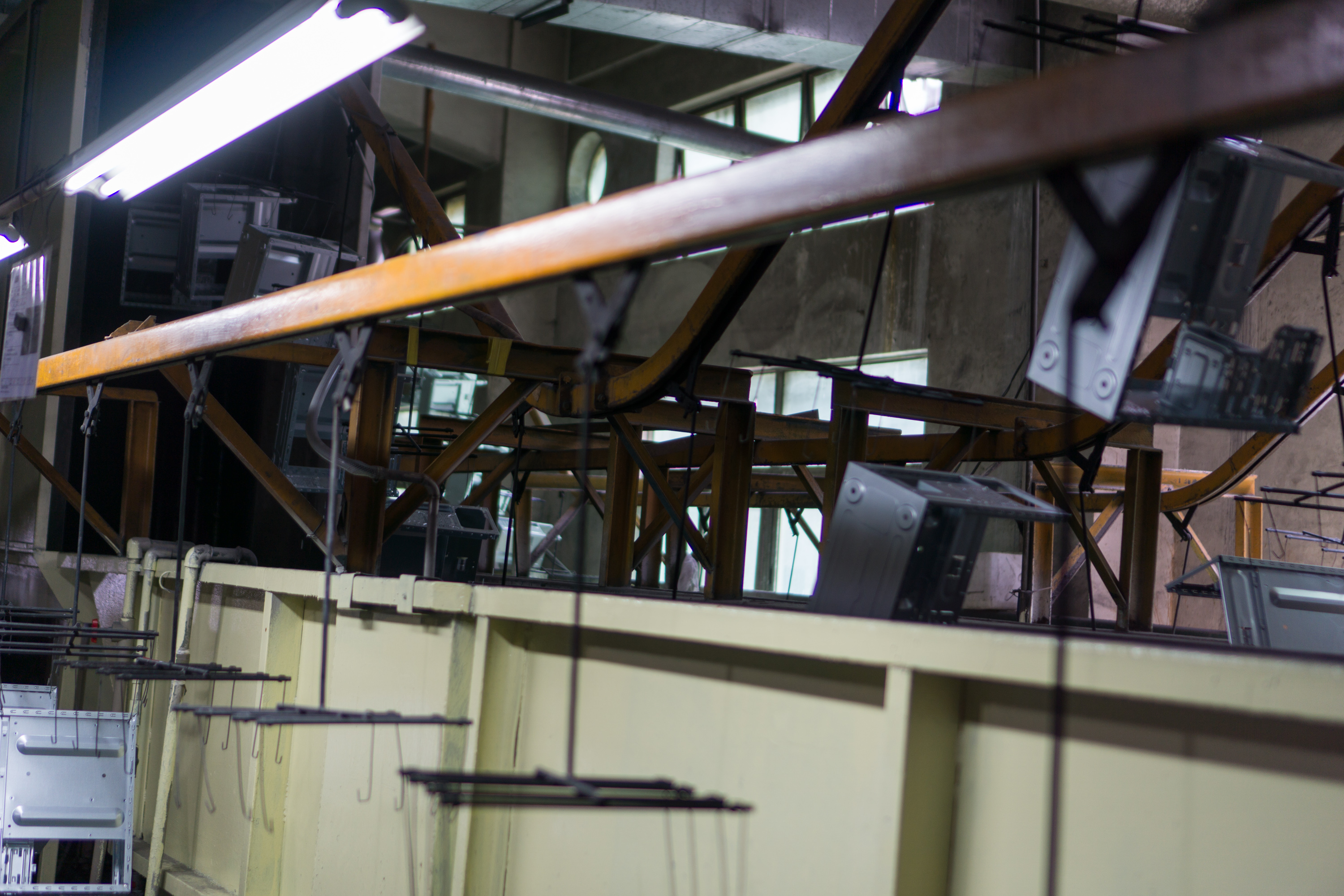
The painting process begins with the case parts, hanging on hooks, descending into a two-step chemical bath. This is to ensure they're clean of dirt, dust, oil, and other contaminants that could affect the evenness of the powdered paint that will soon be applied.
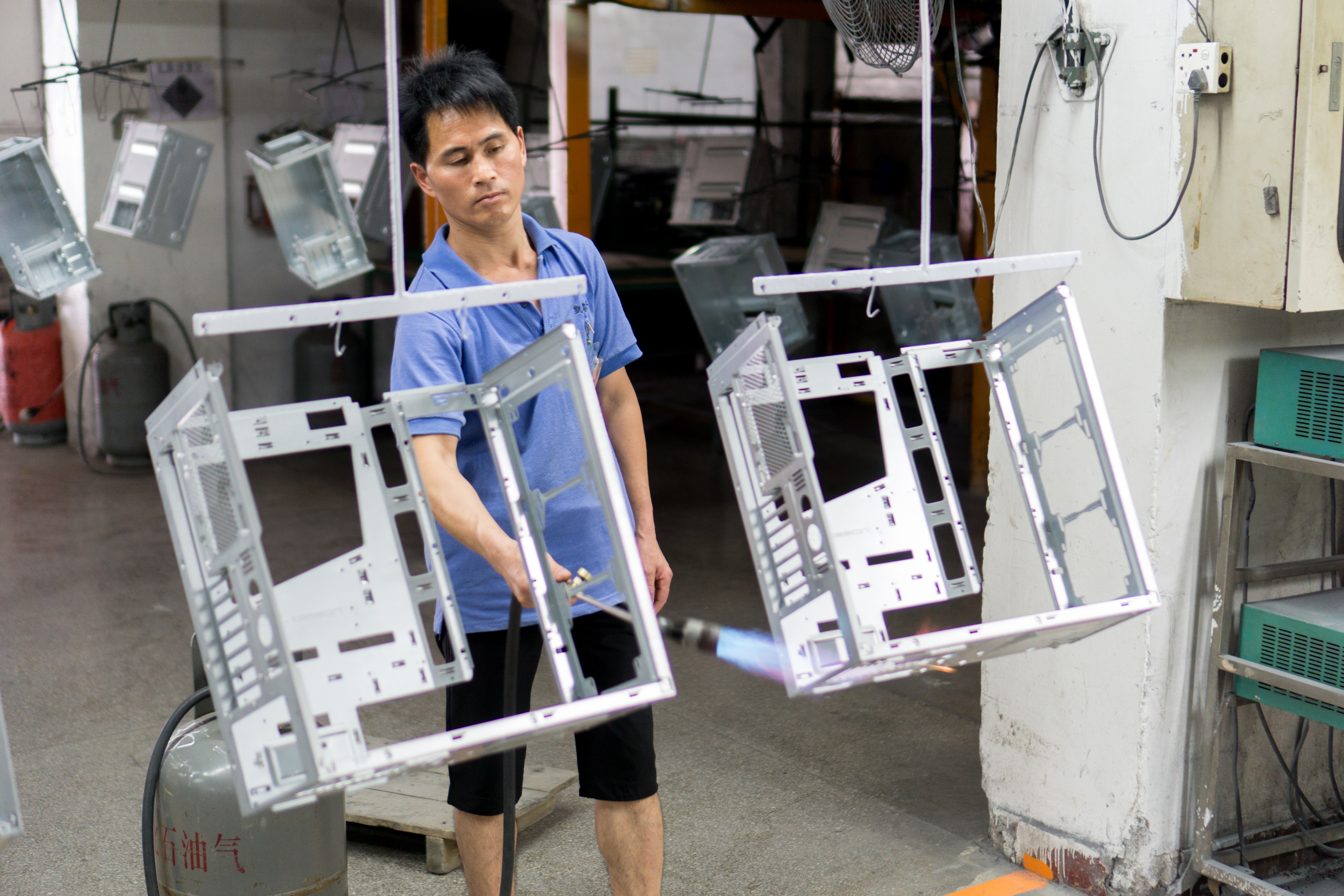
Though they've already been cleaned by the chemical solution, the metal parts are still given one last cleaning before entering the painting chamber, this time by fire. The blowtorch burns off any remaining dust or debris.
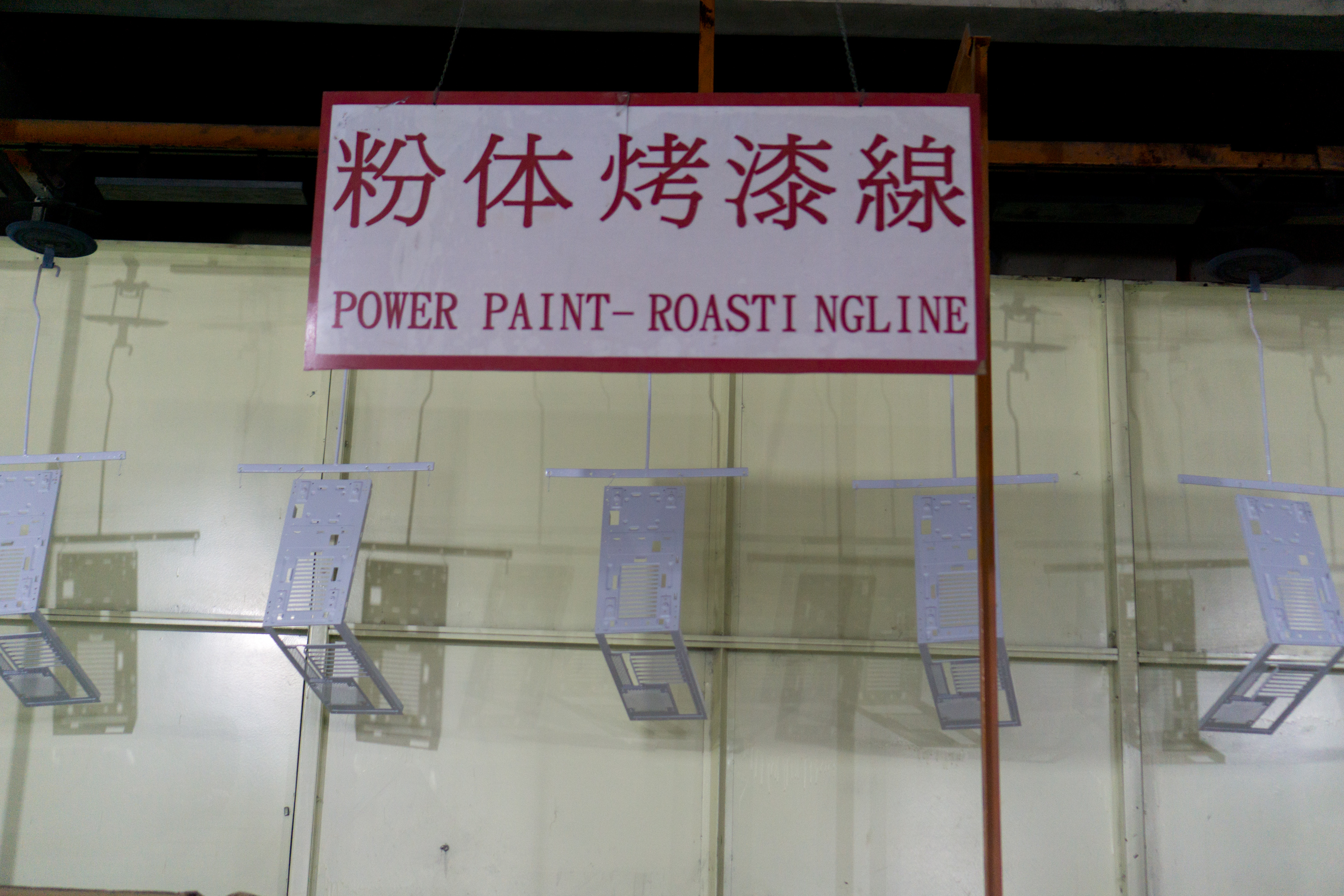
Kerning isn't this sign's strong suit, but it gets the message across.
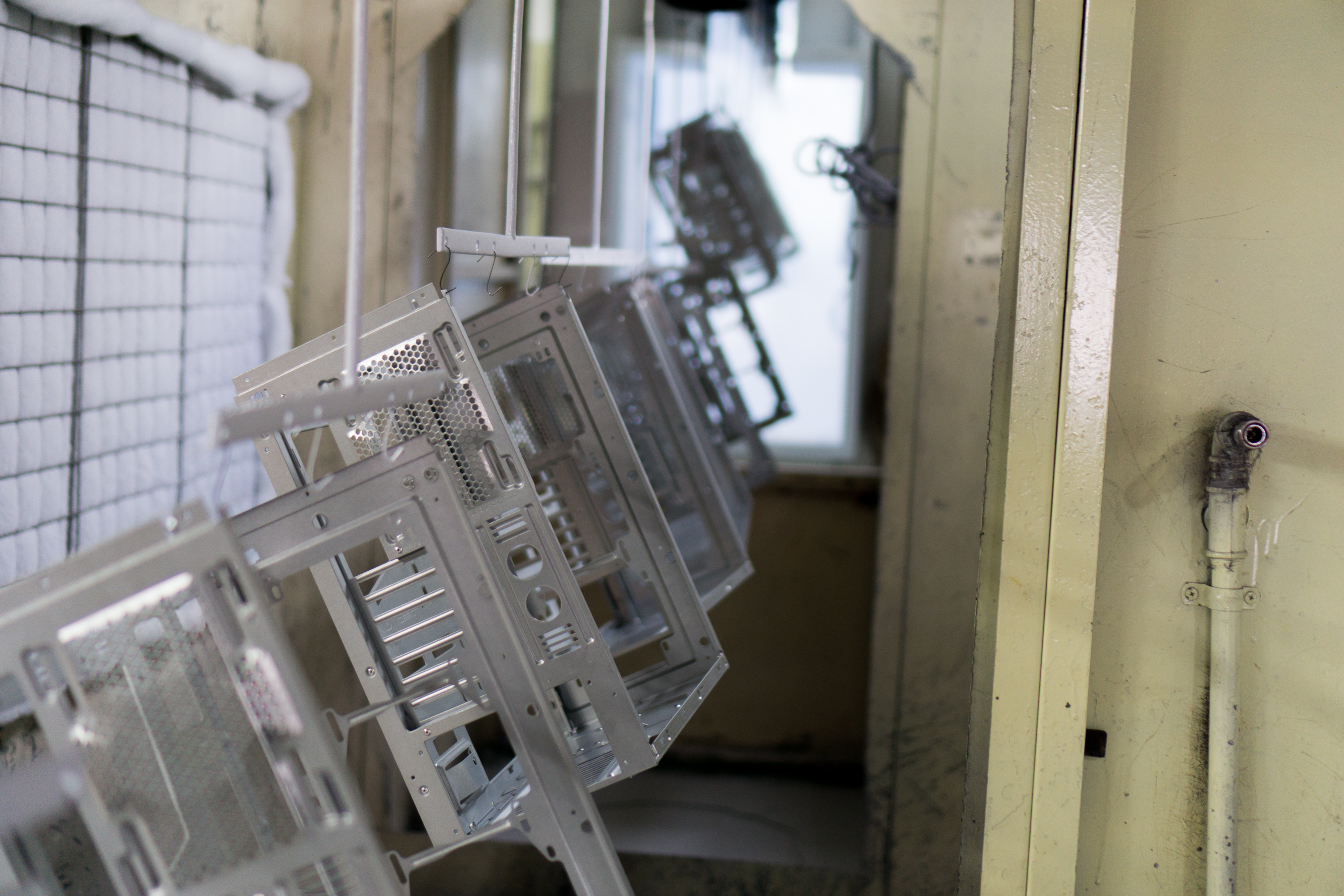
After a good blowtorching, the cases enter into an automatic painting chamber, which coats them in powder paint.
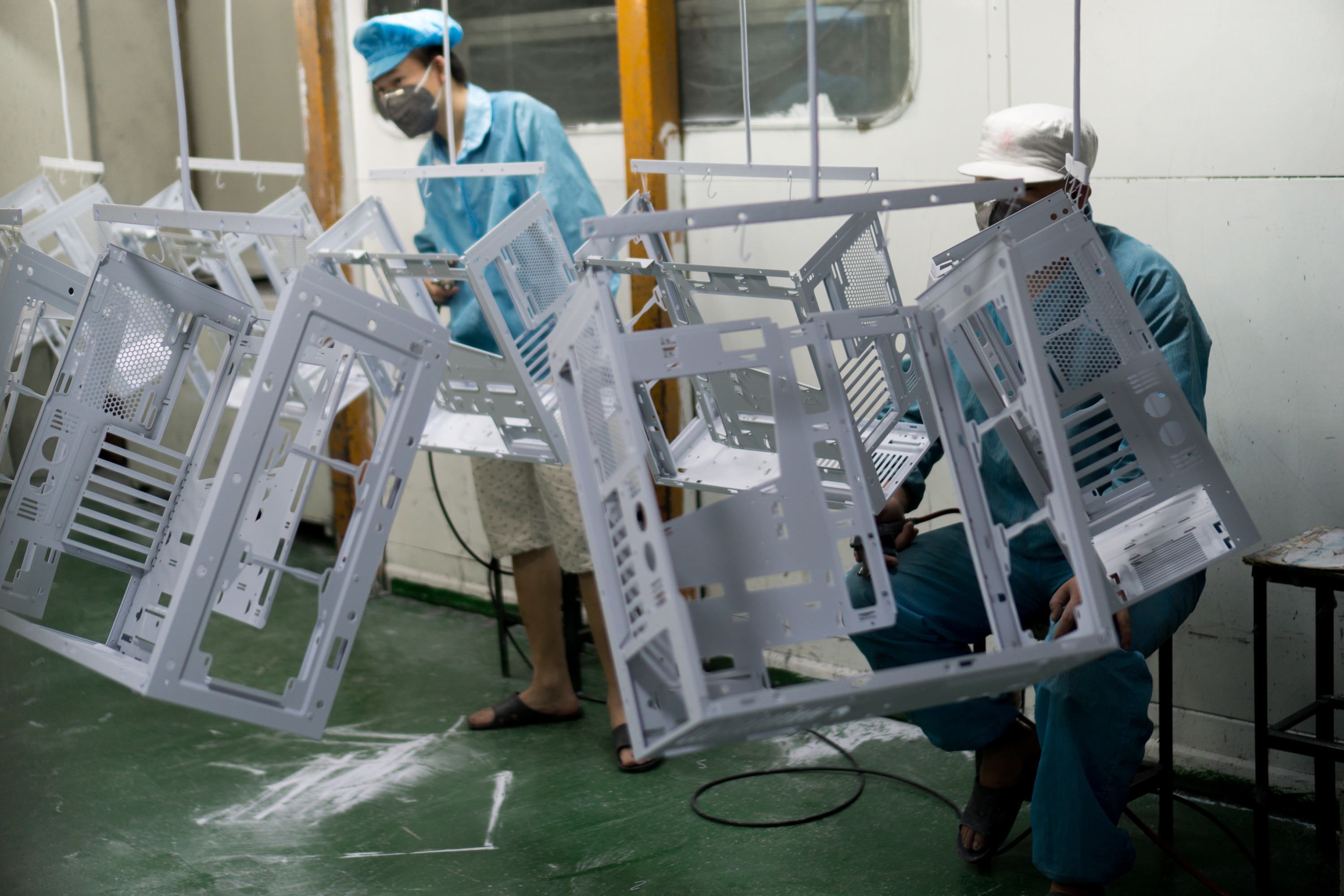
The automated paint process is good, but it isn't perfect. To ensure the coat is even and to get paint into every nook and cranny, workers in the paint chamber spray in spot corrections.
You may have noticed that there aren't many white cases on the market compared to black or other colors. This is because white is the most difficult color to get right and matched. For example, it's nearly impossible to match white-painted metal to perfectly with white plastic. Even if possible, the plastic would change color over time. For this reason, not that many companies want to spend the time or effort producing well-made white cases.
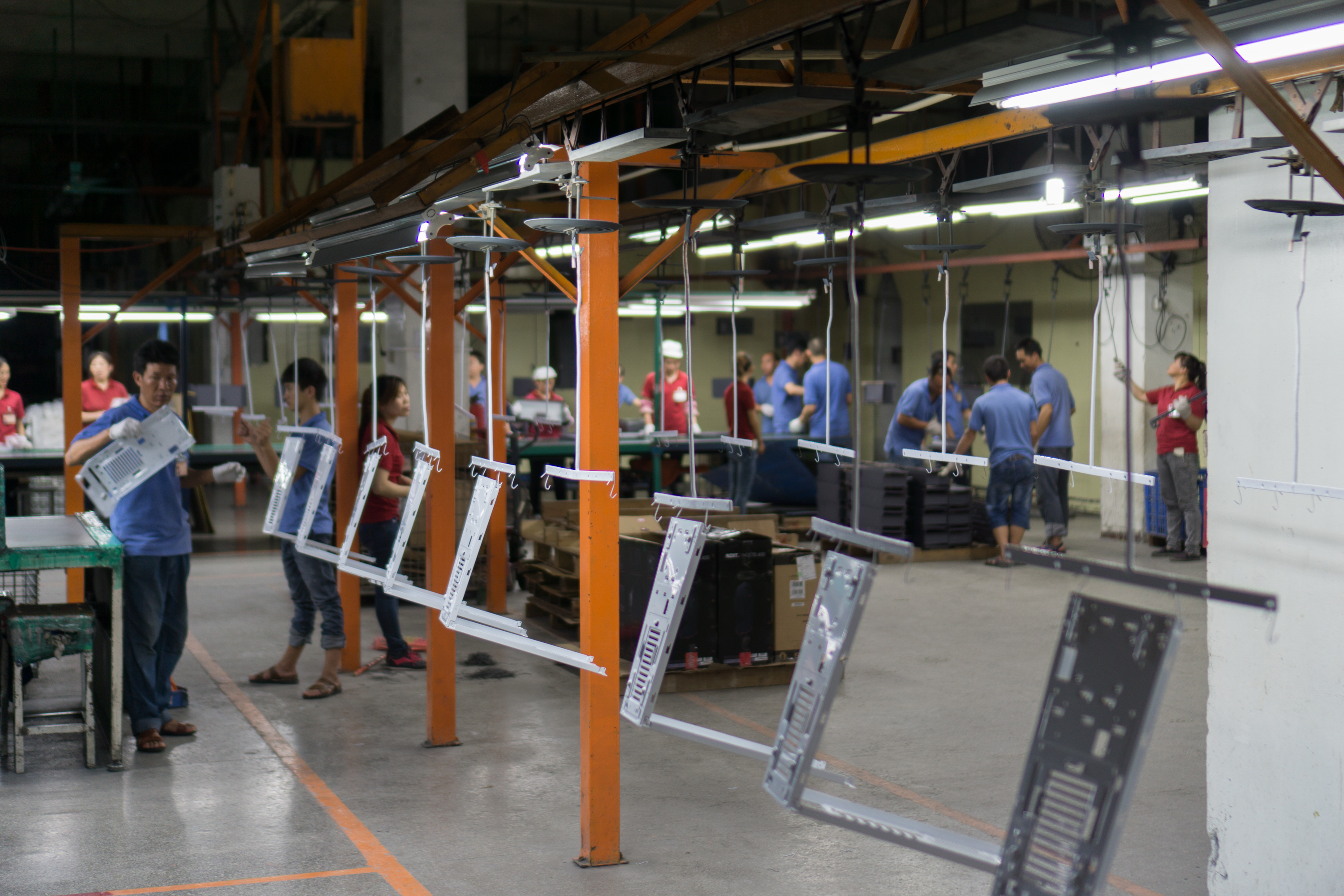
A good look at the hanging hook system that moves components from one paint station to another. The line rotates slowly, moving hundreds of components at a languid pace. This railway snakes around a huge area of the warehouse, around multiple corners before arriving at this point.
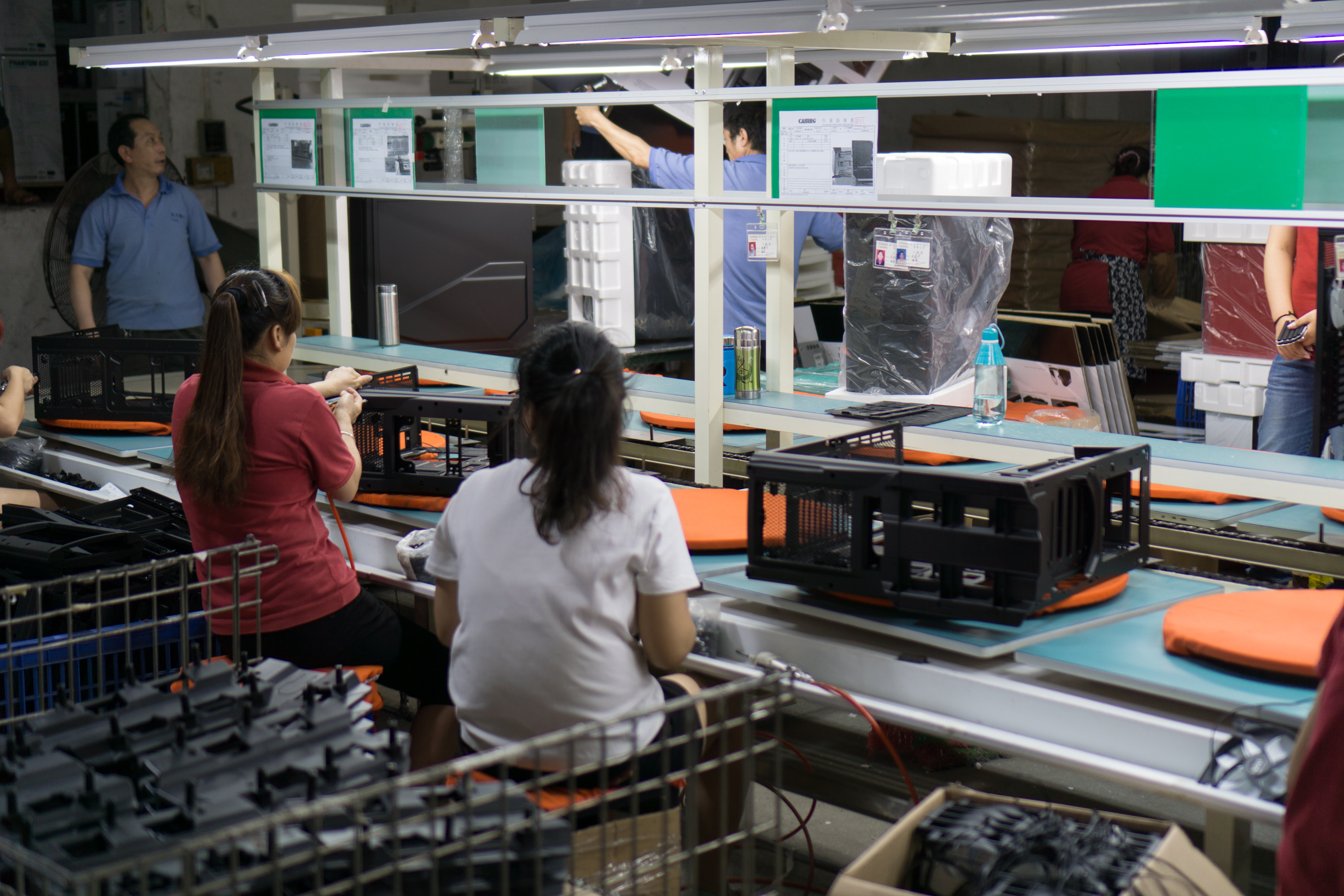
Next to painting lies the final step of the process: assembly! There are many workers every step of the way, but this is probably the most manual labor-intensive area of the factory. Everyone sitting on this row has a specific piece to install or parts to screw together.
With the entire factory working in harmony, NZXT can produce around 200 cases per hour. That's for smaller and simpler cases, though—the case being built here, the Phantom 820, is a different story. The factory can only produce between 50 and 60 of these per hour, since it's a larger case.
Because production speed varies between cases, there's no set number of products that roll off the assembly line in a given day. What's being produced will change from day-to-day, too, based on orders from retail partners like Newegg, existing warehouse stock, and projections for what cases will soon be in demand.
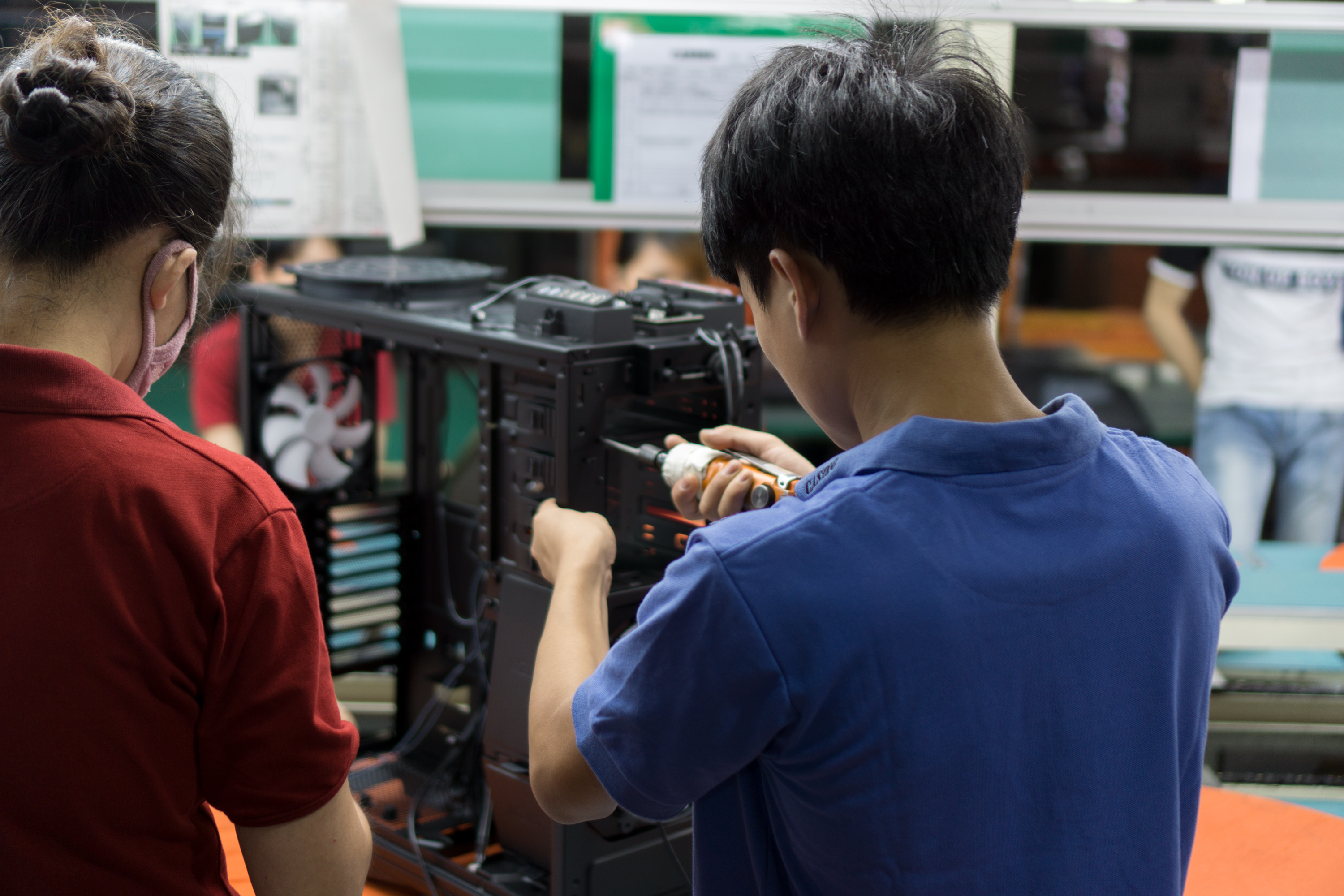
An electric screwdriver makes short work of screwing in the back panel of the case.
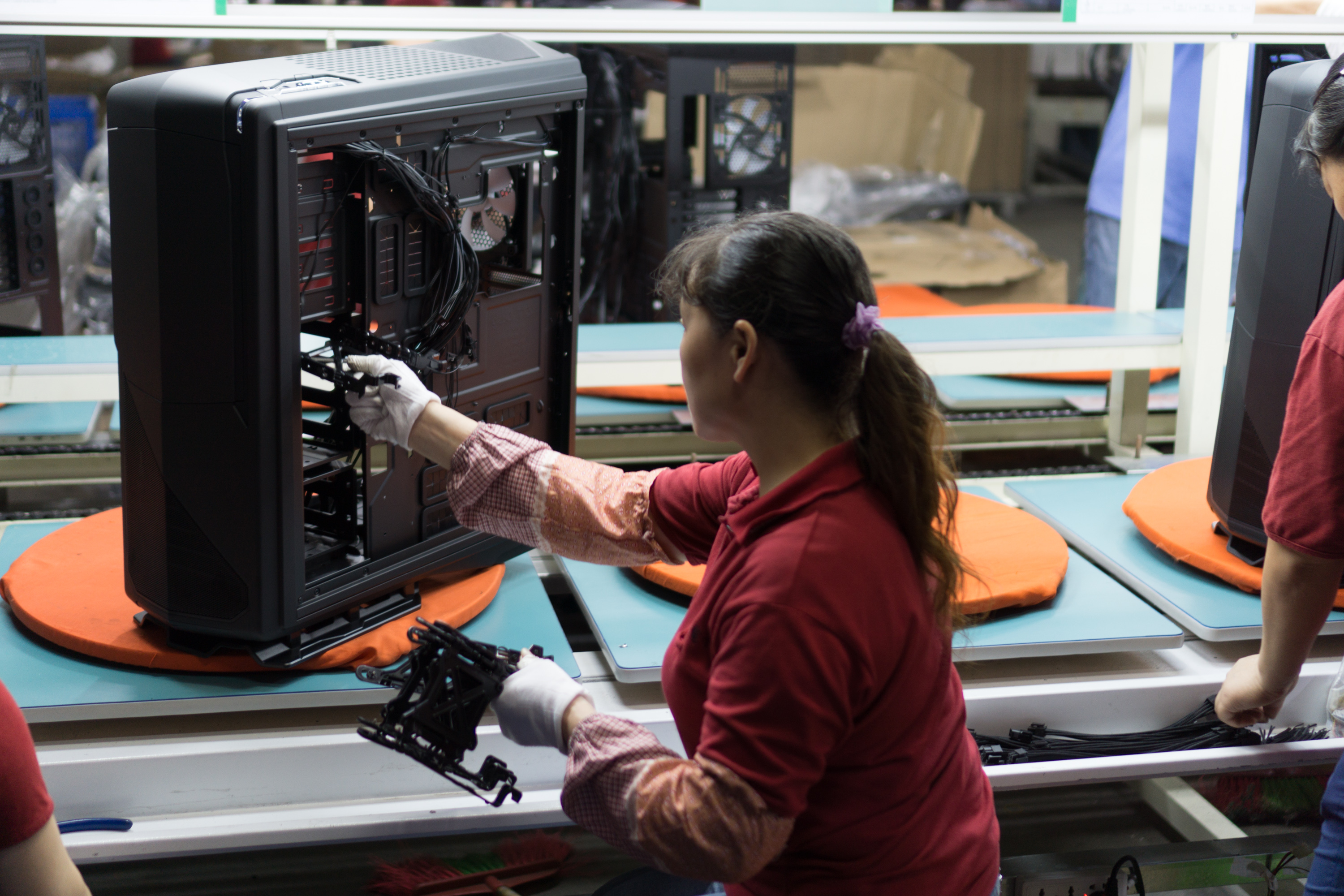
This worker slides drive trays into a nearly finished Phantom 820 case.
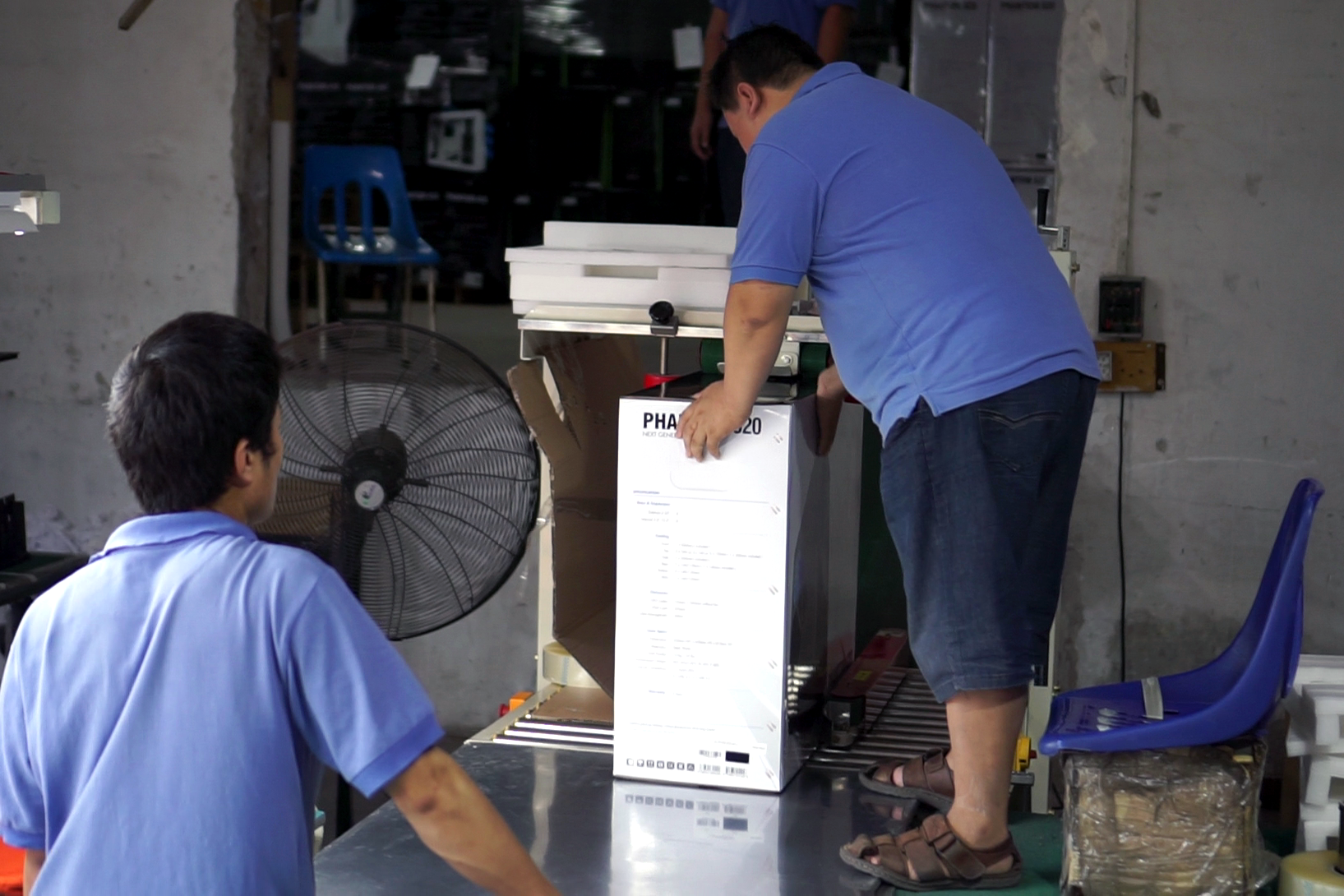
Once the cases are fully assembled, they're on to the last step. Wrapped in plastic, styrofoam blocks are mounted to each side, and then workers place a box around the case, toss in the manual, and run it through an industrial tape machine and straight up the conveyor belt to storage. There are stacks of cases in the back waiting to be shipped out.
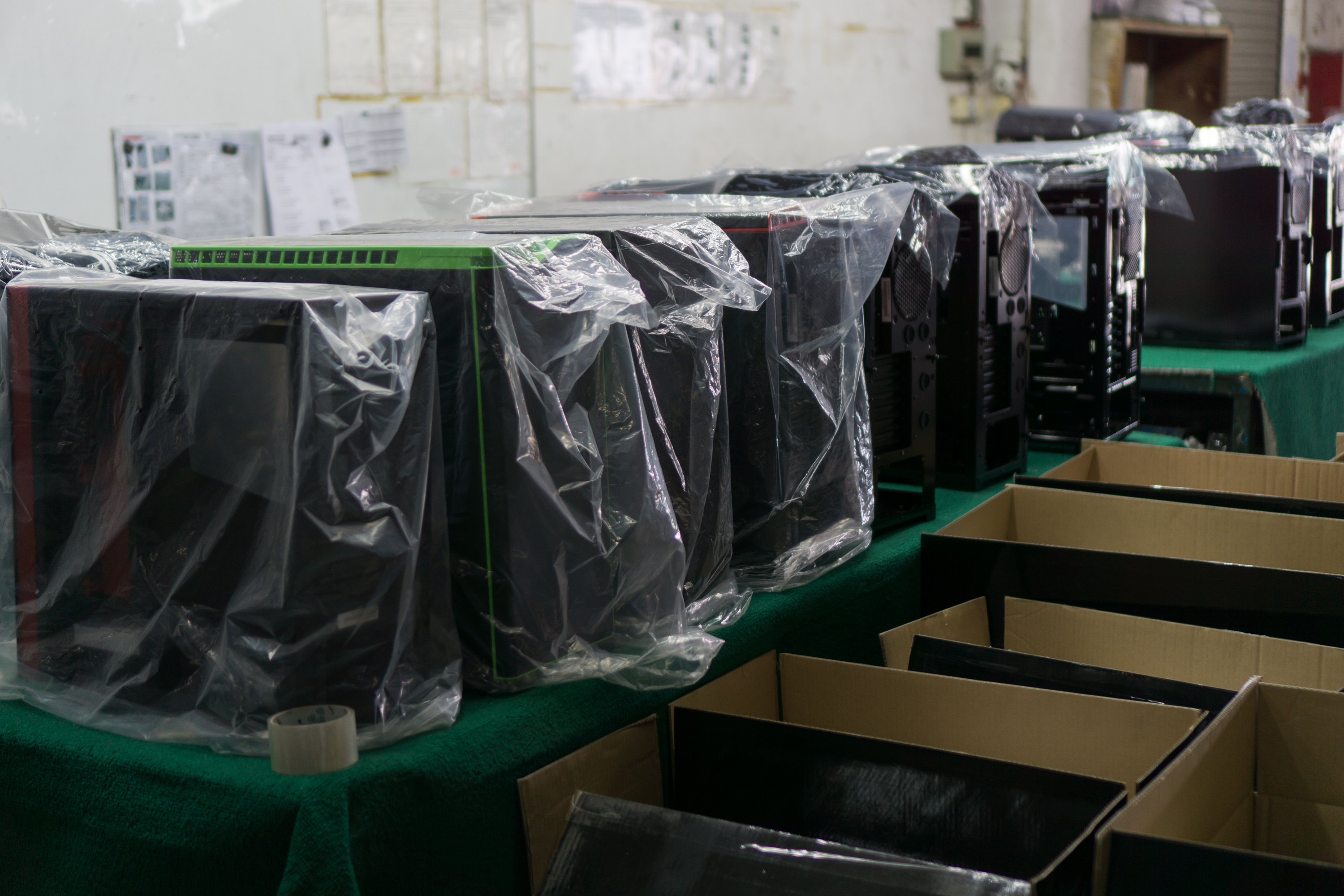
Even after cases are completely assembled, wrapped, and packaged into a box...they're not always completely finished at the factory. At the final QC station, workers randomly select cases to remove and check for any manufacturing issues.
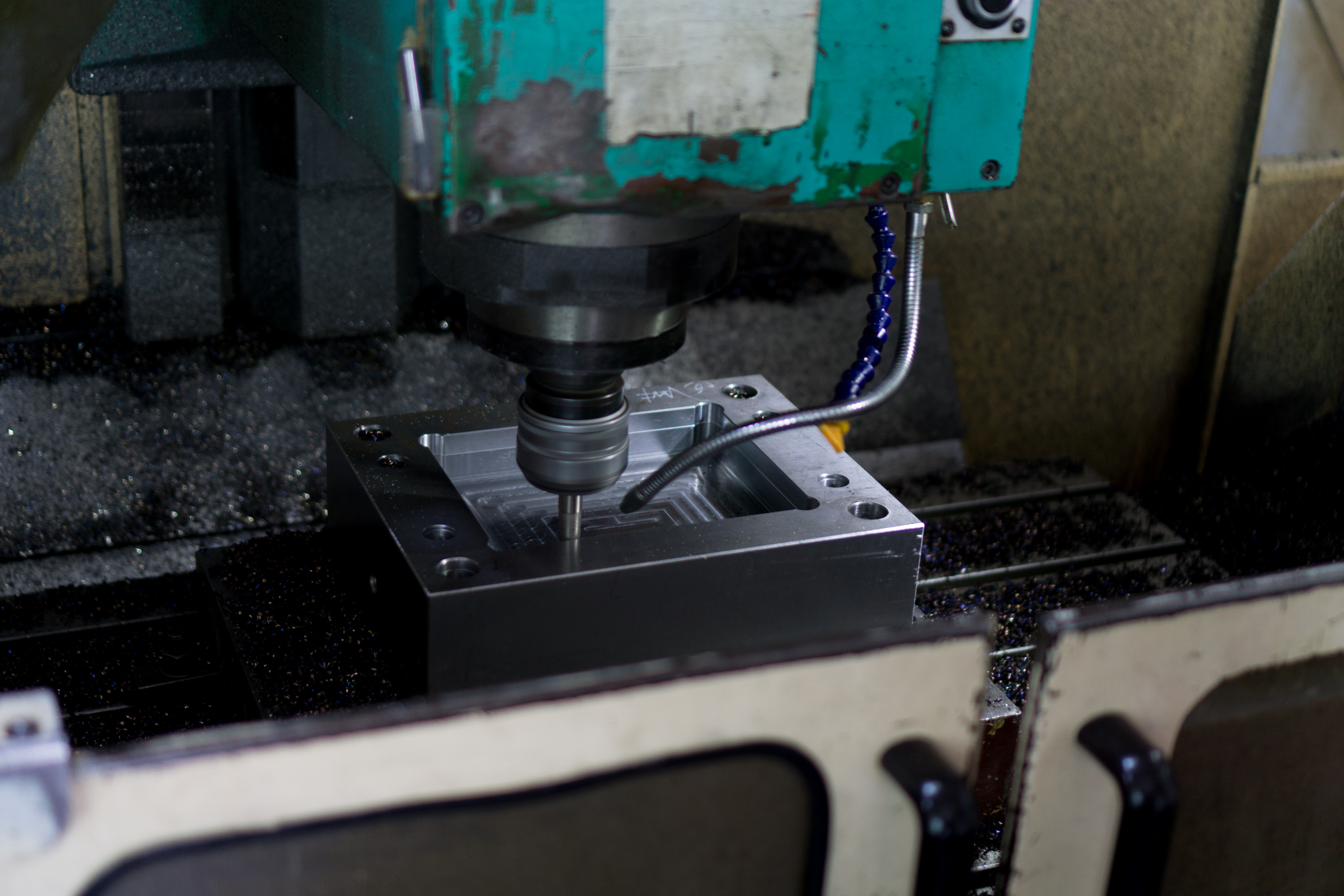
At the beginning of the tour we saw toolings for metal components being made. Here a drill is creating another type of tooling, this one for plastic. Water is constantly run over the drillbit to keep it from overheating.
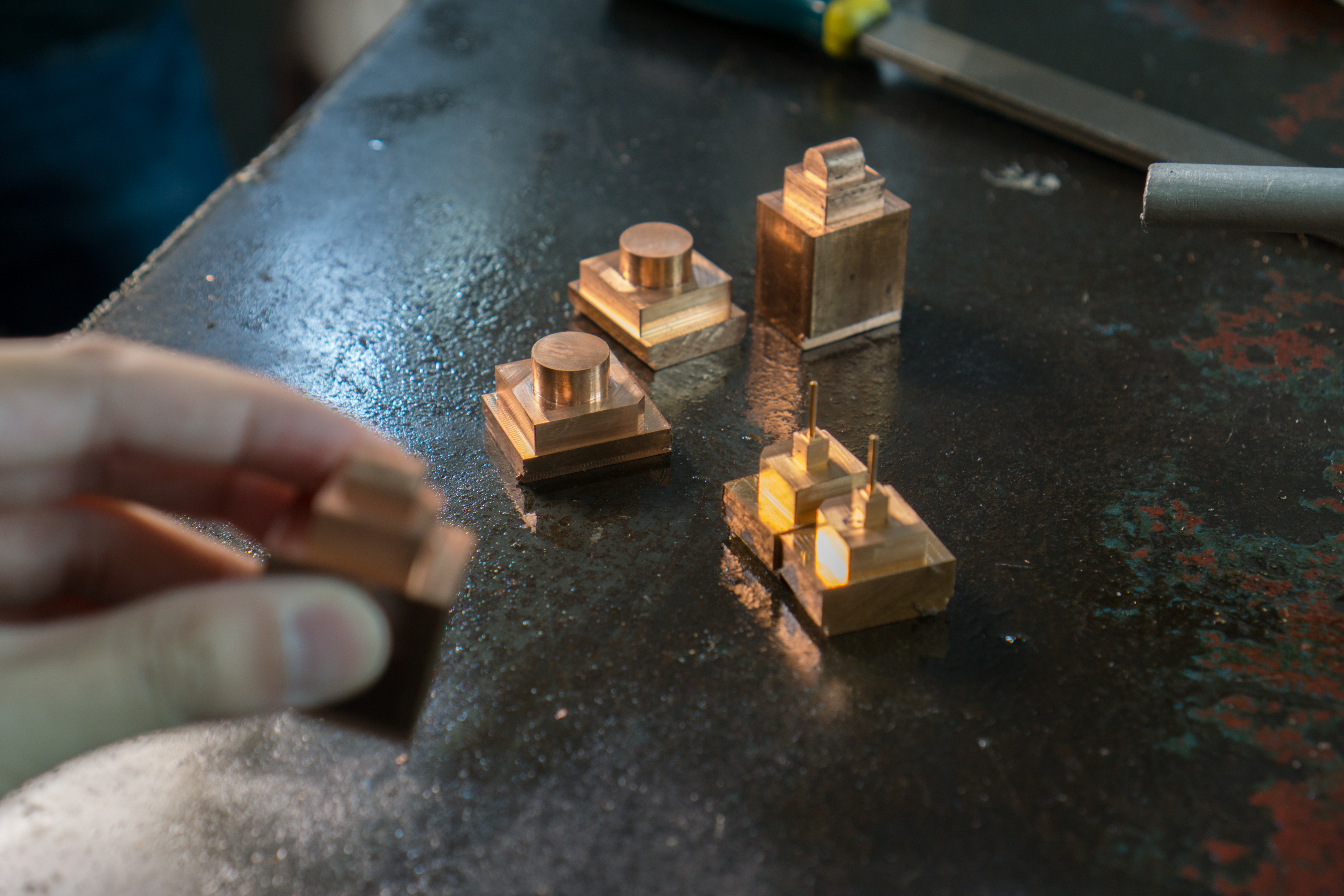
Here are some of the resulting plastic toolings, used to punch out small, delicate shapes in plastic components. As you can imagine, the cuts to form these toolings have to be extremely precise—down to .005mm.
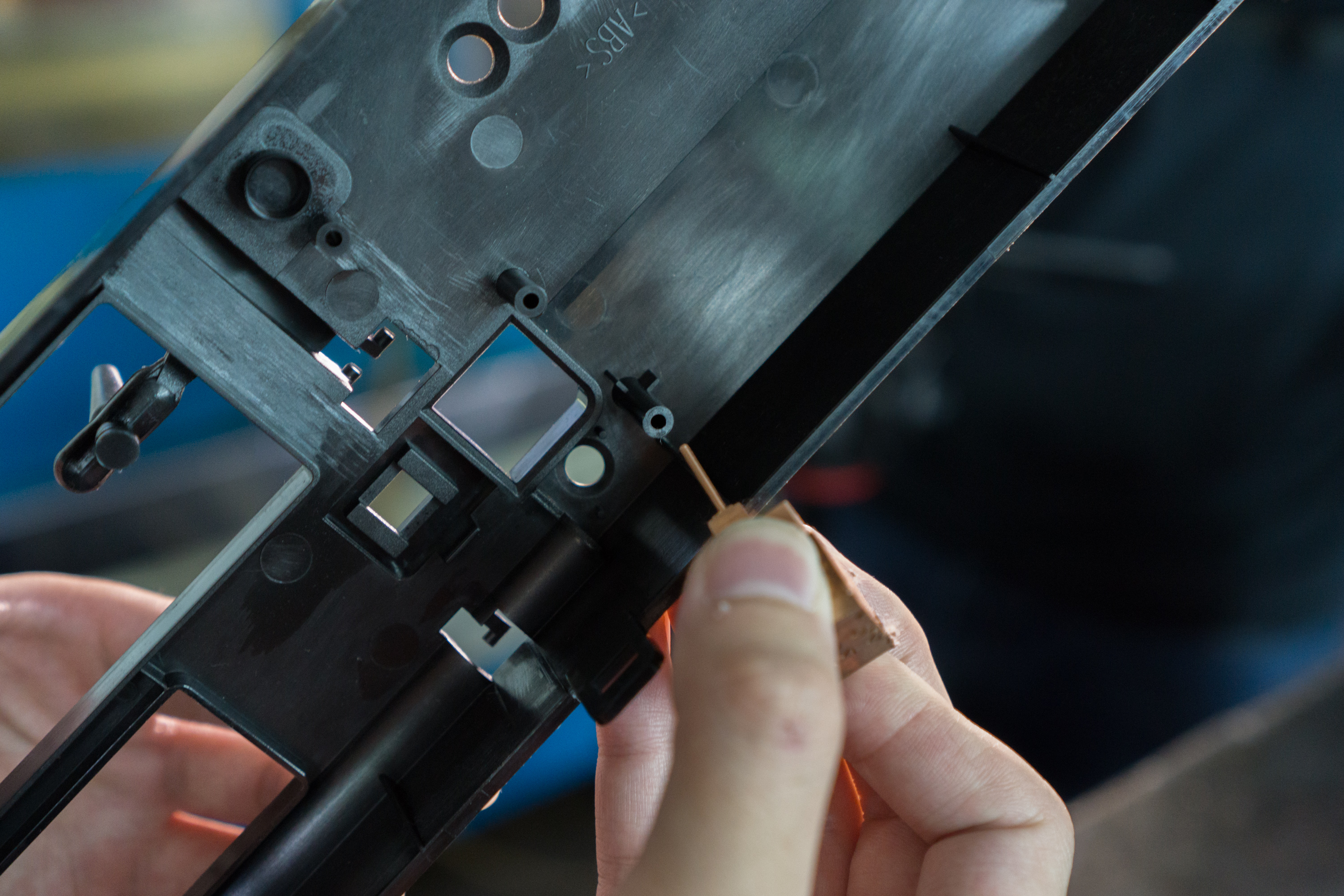
An example of the shape one of the toolings creates in a PC panel.
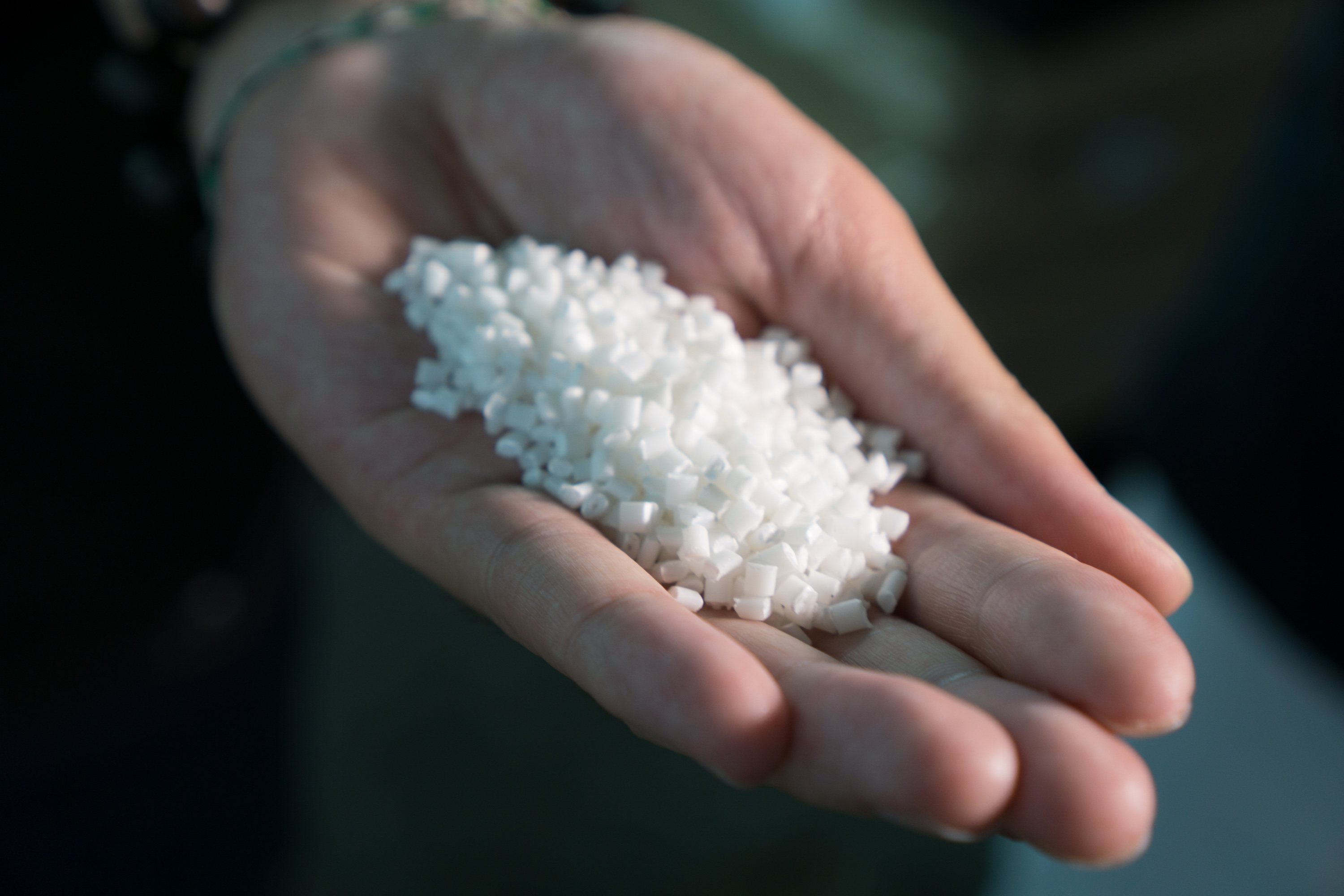
ABS plastic pellets, used to form plastic parts like the one in the previous image.
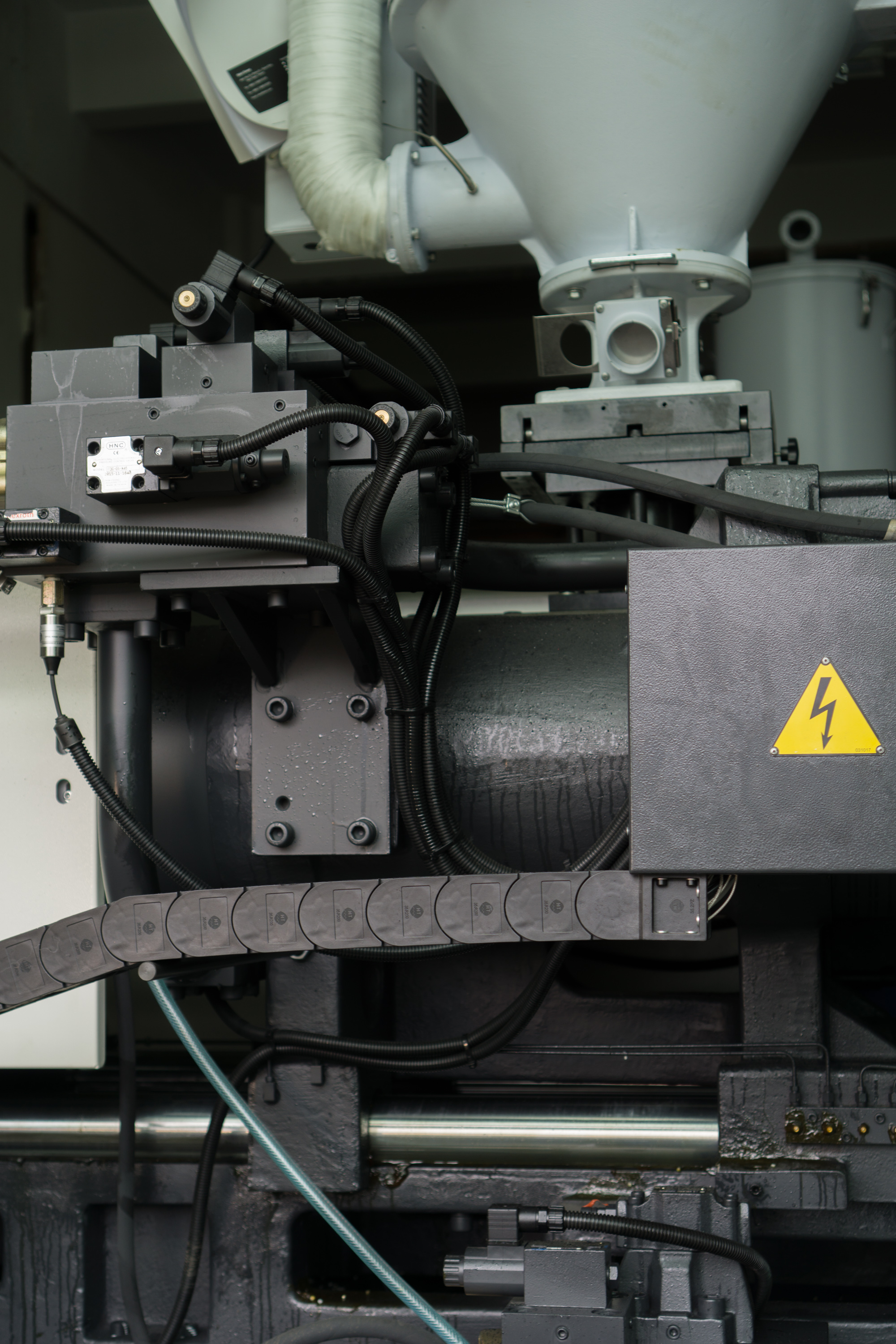
To create plastic parts, the ABS pellets are fed into the white chamber at the top, then heated to temperatures as high as 280 Celsius to melt them. the melted plastic is then injected into a tooling to form a part.
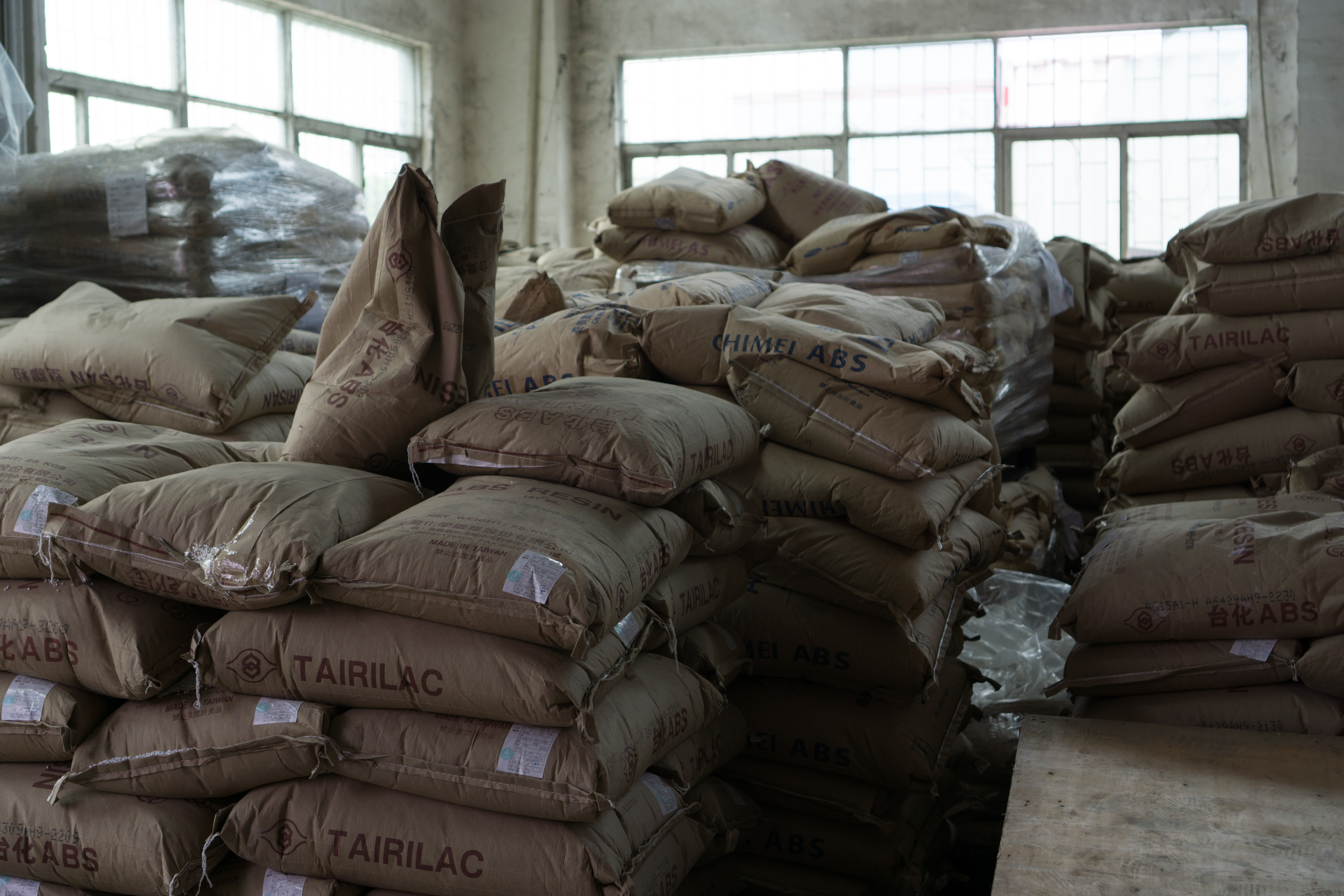
There's a lot of ABS plastic in storage, waiting to be used.
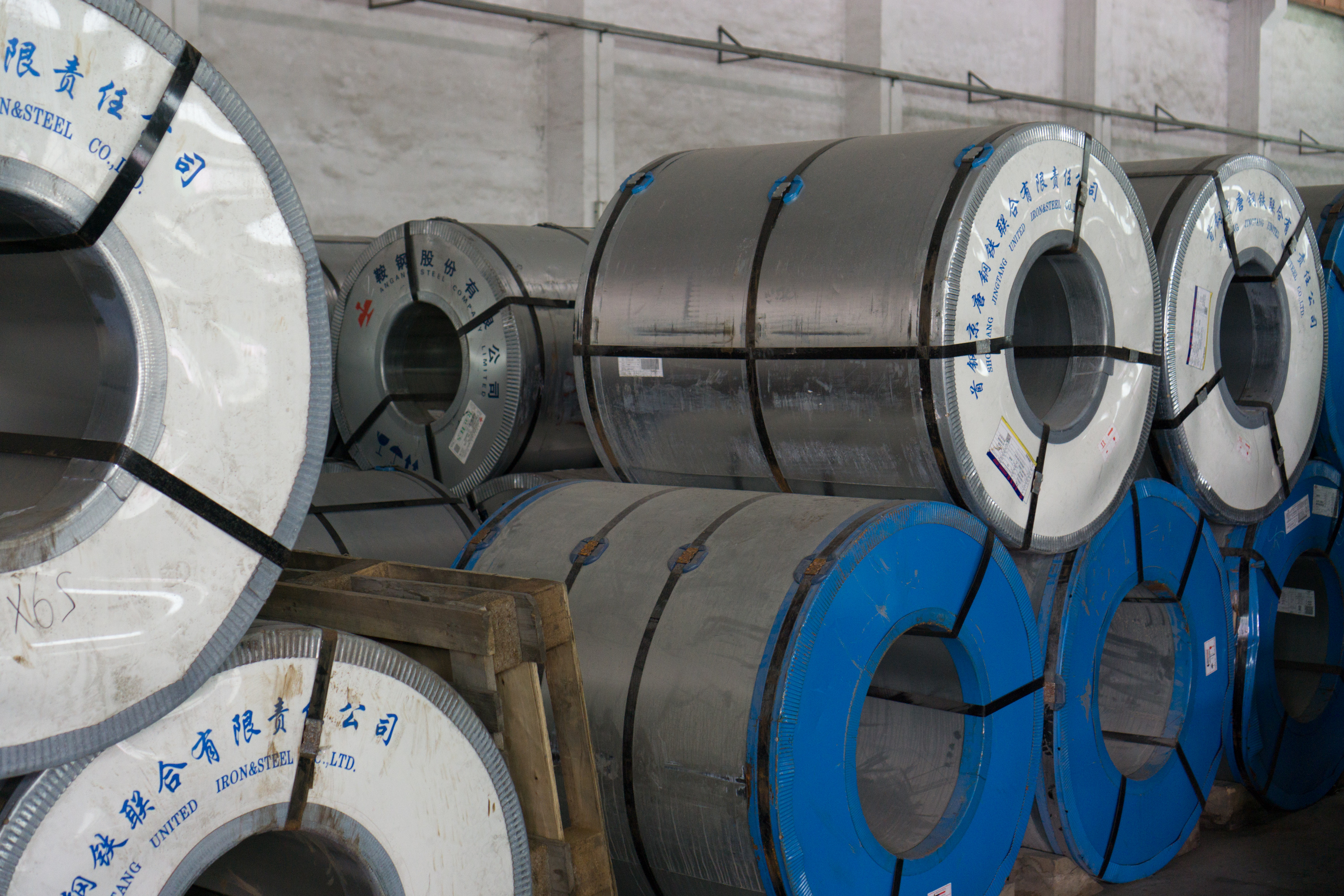
Steel rolls waiting to be turned into PC cases. Each of these rolls weighs 660 kg (about 1455 pounds) and costs around $2500.
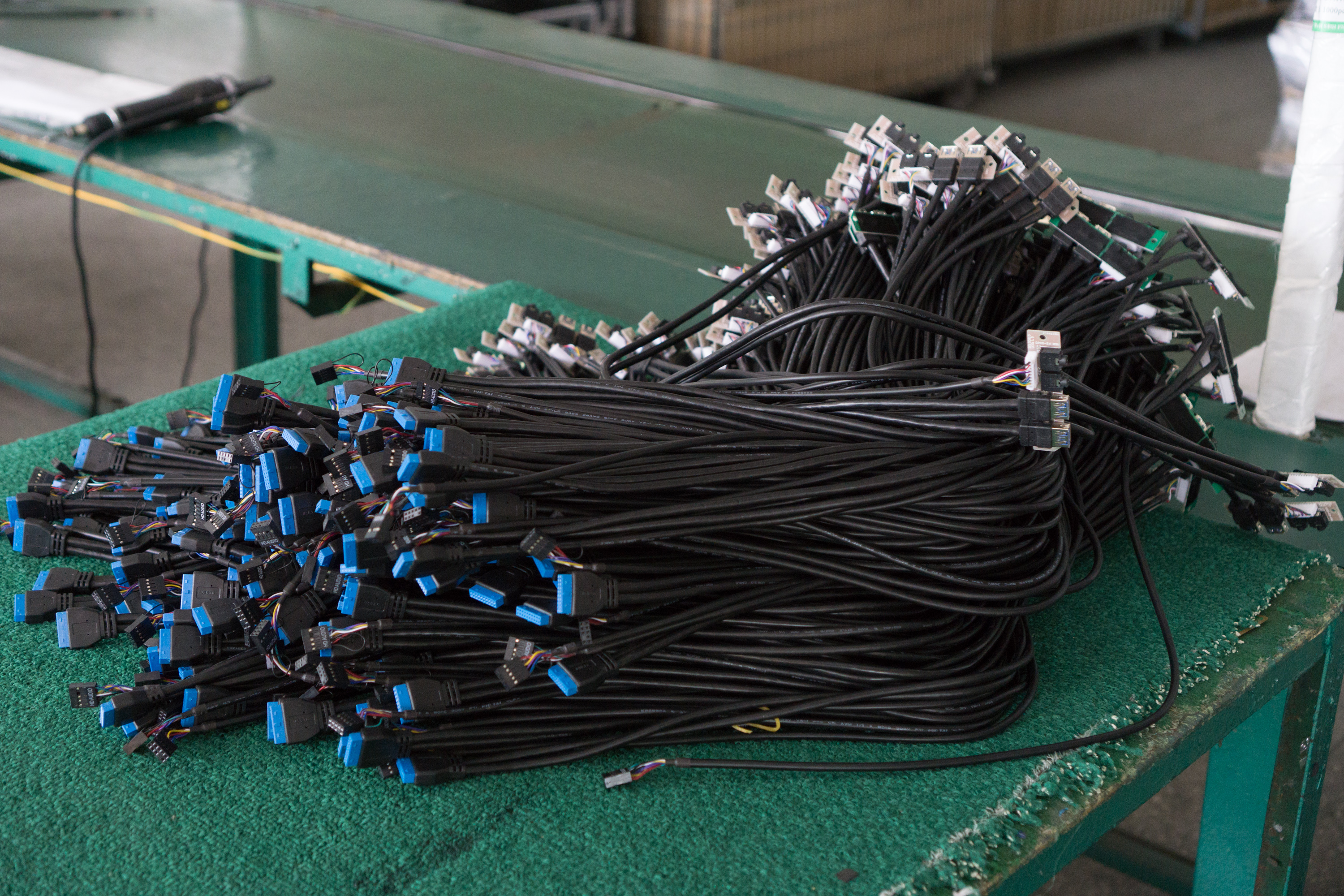
Spare USB cables and front panel connectors randomly spotted on a table near the steel and plastic storage. Never know how many you'll need!
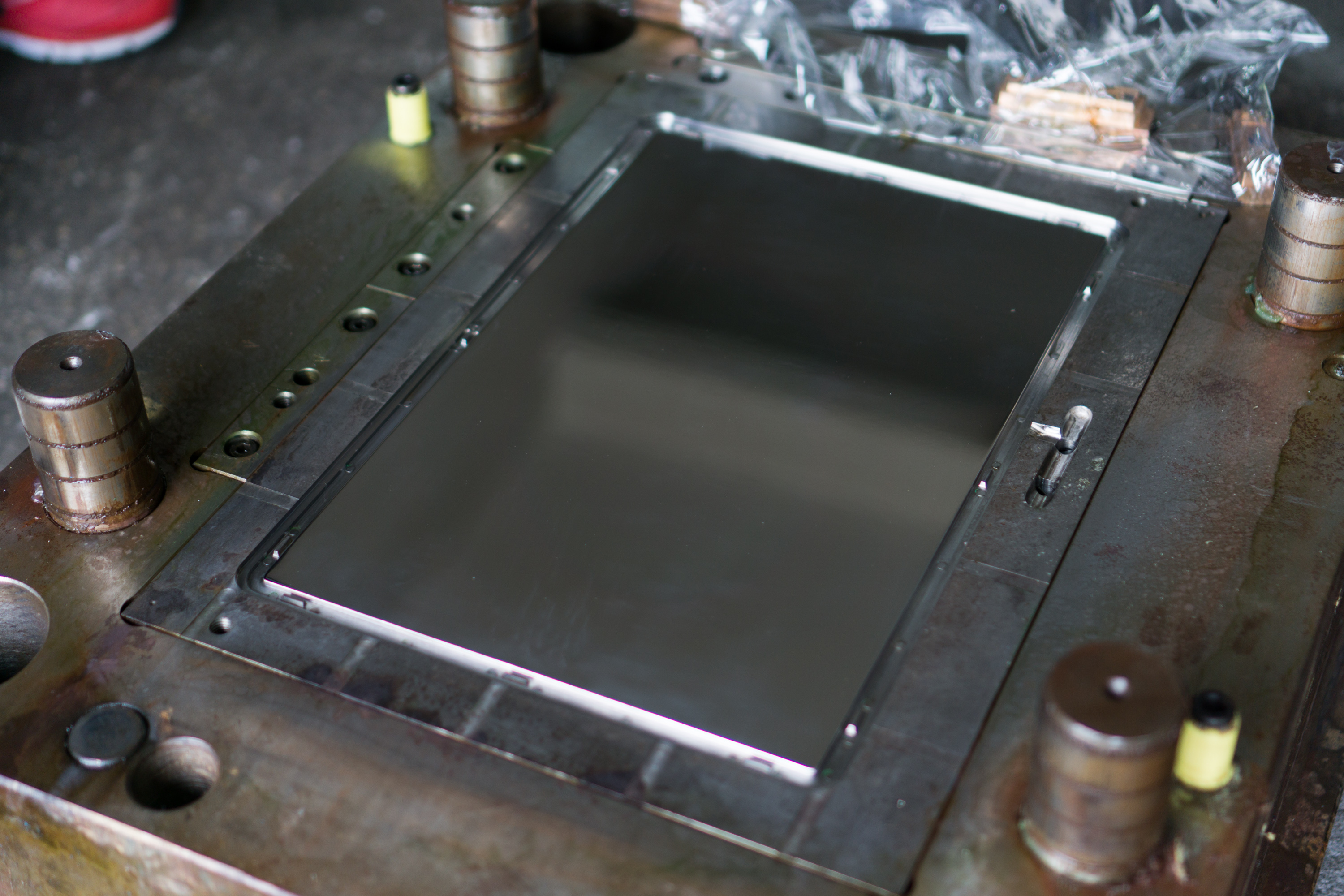
Remember the plastic injection molding machine a few slides back? This polished tooling is an example of what that plastic would be injected into. But it's a bit special: this is for a clear plastic side panel, which is why the metal is so shiny. That panel needs to come out clear.
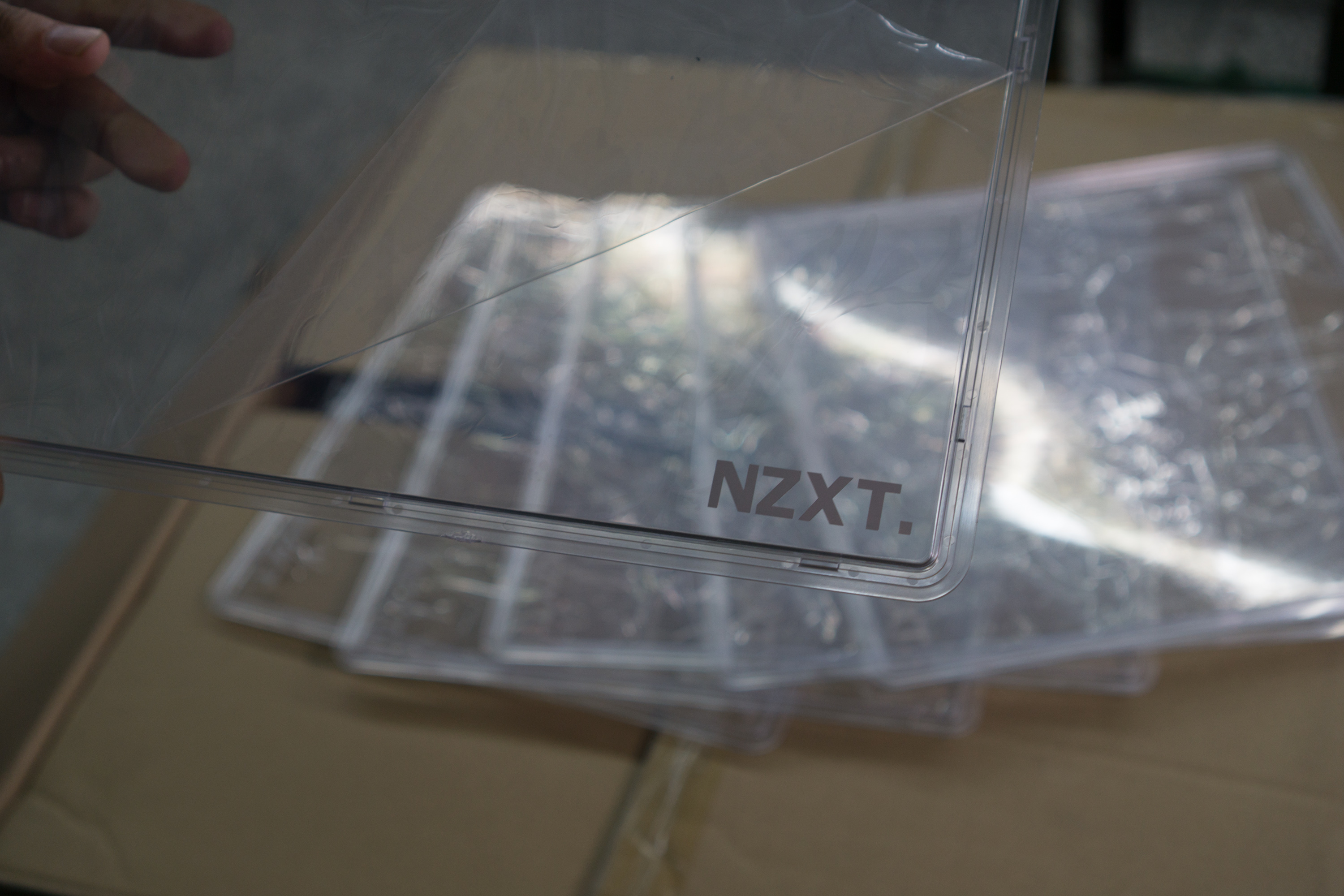
And the final product, with a decal attached. Nice and clear!
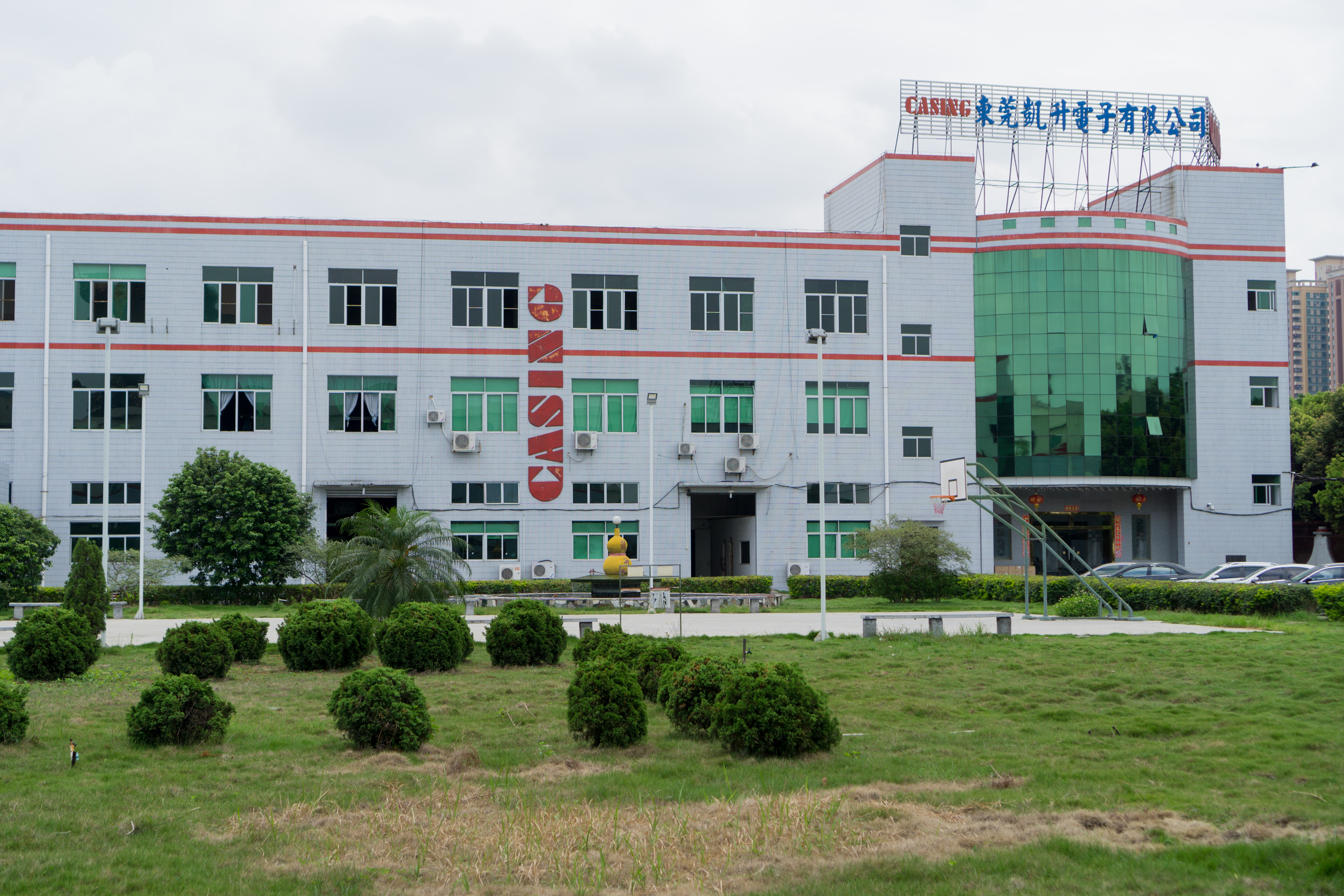
And that's it for our tour of NZXT's case warehouse! We definitely left with a greater appreciation for how much manual labor is involved in producing each and every case. Stay tuned for a video tour of the factory coming soon, and some more behind-the-scenes hardware features. Here are some more to check out:
Inside Logitech: how gaming mice are built and tested
Inside Logitech: how headsets are designed and tested
How motherboards are made
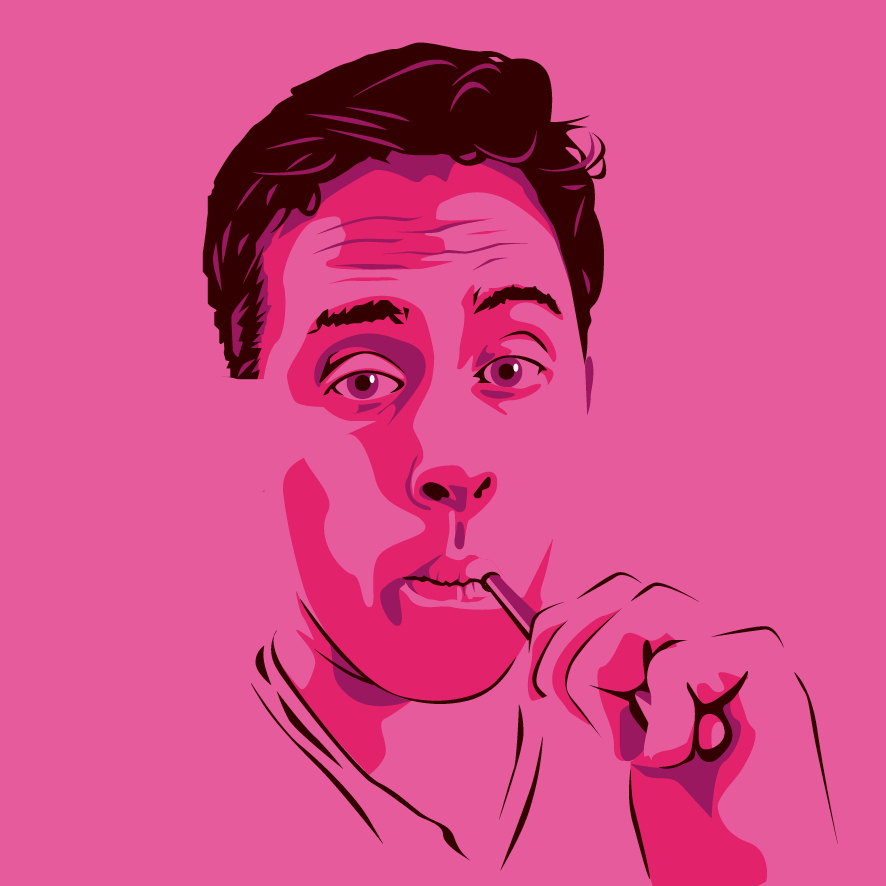
Wes has been covering games and hardware for more than 10 years, first at tech sites like The Wirecutter and Tested before joining the PC Gamer team in 2014. Wes plays a little bit of everything, but he'll always jump at the chance to cover emulation and Japanese games.
When he's not obsessively optimizing and re-optimizing a tangle of conveyor belts in Satisfactory (it's really becoming a problem), he's probably playing a 20-year-old Final Fantasy or some opaque ASCII roguelike. With a focus on writing and editing features, he seeks out personal stories and in-depth histories from the corners of PC gaming and its niche communities. 50% pizza by volume (deep dish, to be specific).